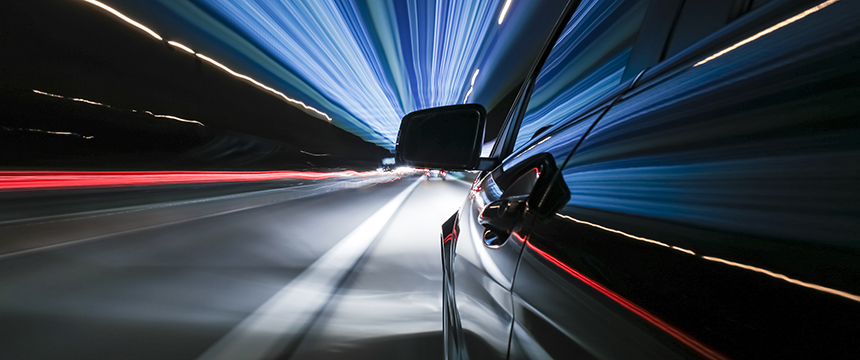
Table of Contents
- Expect the Unexpected: Approaching Raw Material Shortages, Labor Issues, and Freight Increases and Delays in 2022
- Essential Compliance Updates for Multinational Automotive Companies
- NHTSA and Motor Vehicle Safety – 2022 Developments
- 2022 Antitrust Outlook – Significant Changes Under the Biden Administration
- Nearshoring Trends and Important Considerations When Looking to Mexico
- Key Employment Issues Facing Employers in the Automotive Industry in 2022
- OEMs Expanding Suppliers Responsibility for Ordinary Warranty Claims
- Possible Silver Lining: Targeted Acquisitions
- Preparing for Automated Vehicle Regulations and Enforcement in the Face of Stalled Legislation in 2022
- EV Outlook: Market, M&A, Supply Chain, and Regulatory Trends
- Driving Sustainability: Automakers Look Beyond Electric Vehicles
- Putting Brakes on Cybersecurity Threats: Practical Strategies to Mitigate Cybersecurity Risk
Expect the Unexpected: Approaching Raw Material Shortages, Labor Issues, and Freight Increases and Delays in 2022
I. Introduction
AUTHORS | |||||
Ann Marie Uetz | auetz@foley.com | |||||
Vanessa Miller | vmiller@foley.com | |||||
Nicholas Ellis | nellis@foley.com |
In 2022, automotive suppliers face many of the same issues that have bedeviled the industry throughout 2021, as well as a host of all-new challenges. Unfortunately, as with many aspects of pre-pandemic life, the relative stability in the global supply chain that the automotive industry enjoyed for many years is unlikely to be restored any time soon. Suppliers must be agile and adapt to these new and continuing challenges.
This article highlights several key areas of focus for suppliers looking ahead, including seeking greater flexibility and risk sharing in pricing, warehousing/inventory, and managing freight costs. Among other strategies, suppliers should consider updating many of their traditional operational and contracting practices in order to enhance flexibility in a more unpredictable world. While the changing landscape presents challenges, it also presents opportunities for growth. The suppliers that best adapt will be the companies that are positioned best to thrive going forward.
II. The State of the Automotive Supply Chain as We Enter 2022
For many automotive suppliers, 2021 was a year defined by shortages, increased costs and other unprecedented supply chain challenges. The lockdowns of 2020 quickly gave way to shortages of many raw materials and components, as supply could not keep up with surging demand. While the global shortage of semiconductors may be the most publicized of these issues, many suppliers also faced difficulty in obtaining other materials, including steel, resin, and foam. In keeping with the law of supply and demand, these shortages quickly turned into rapidly escalating costs for many suppliers, with hefty price increases that were not contemplated in suppliers’ quotations, and in many cases they were not expressly covered by their supply contracts.
In addition to difficulty obtaining materials, automotive suppliers faced significant operational and logistical hurdles. Suppliers encountered and continue to face difficulties in obtaining sufficient labor to keep their plants running at full capacity. Suppliers also had to contend with myriad logistical challenges, including port delays, the Suez Canal blockage, a dearth of containers, a scarcity of truck drivers, and massively increased costs for shipping. The cost of shipping containers from Asia to the United States soared, reaching in excess of a 500% increase from just a year earlier.1 Suppliers also faced surging costs for labor. Under the burden of these significant challenges, the automotive supply chain exchanged a fresh wave of force majeure declarations and notices of commercial impracticability. Unlike the case in 2020, when most of the automotive industry shut down in unison, such declarations often were the subject of significant disputes as parties wrangled over responsibility for costs and tried to maintain operations.
Compounding these difficulties, many suppliers’ efforts to manage their supply chain were further complicated by the actions of their OEM customers. Faced with shortages, many OEMs reacted by ramping up their releases to unrealistic levels far in excess of the original EDI projections, leaving suppliers trying to divine what were the “real” quantities that ultimately would be needed. OEMs also reacted to the shortage of semiconductors (and other inputs) with unpredictable rolling shutdowns of production. Many suppliers experienced situations in which they had undertaken significant efforts, including potentially expediting shipments in order to meet releases and forecasts for a certain volume, only to see their OEM cancel or reduce releases at the last minute. These issues often left suppliers holding significant inventory and materials without payments from their customers to provide the cash flow needed to pay their own sub-suppliers. Production shutdowns further exacerbated ongoing labor problems. As suppliers were forced to furlough their work force, they could not be sure how many of their workers would return once production resumed.
Unfortunately, 2022 is projected to be another difficult year for automotive suppliers. Many analysts predict that the semiconductor shortage and other supply chain disruptions will continue into at least 2023, even if there are some signs of gradual improvement.2 Such disruptions and shortages are likely to continue to drive costs up. Furthermore, the full impact of the Omicron variant of COVID-19 (and potentially other variants) is not yet known. While there appears to be little appetite for a return to a lockdown in the United States, lockdowns remain a possibility in many other countries. In particular, China has hewed closely to a “zero-COVID” strategy and recently re-imposed lockdowns in a number of cities. A more widespread outbreak in China, or other significant manufacturing locations, poses a risk of further significant disruption in the automotive industry.
III. Strategies for Approaching the Changing Circumstances in the Global Supply Chain
For most of the last two years, many automotive suppliers have operated in some form of crisis management mode as they waited for the return to “normal.” However, it is rapidly becoming apparent (to the extent it was not already apparent) that there will not be a return to the conditions that existed before the pandemic any time soon. COVID-19 will be with us, in one form or another, for the foreseeable future. The era of minimal inflation that has prevailed in much of the world for the last decade appears to be over. For these, and a variety of other reasons, companies likely face a period of greater instability and volatility in the global supply chain. So how can companies shift out of crisis management mode and adapt their business practices to survive, and even thrive, in the new environment? This article presents three key strategies that suppliers should consider, from the contracting stage through operations.
- Focus on pricing provisions and parameters triggering pricing relief. For many years, the standard in the automotive industry has been long-term contracts at a fixed price (or, in some cases, requiring that the supplier provide annual price reductions). In many cases, these contracts locked the supplier into an indeterminate “life of the part”/“life of the program,” leaving the supplier subject to the whims of its OEM customer for years and through an extended service period as well. Provisions allowing a supplier to request a price increase were a rare commodity, with the exception of contracts for certain raw material-intensive components. Suppliers and OEMs alike, having lived through repeated cycles of spikes and declines in raw material pricing, recognized that long-term fixed price contracts for such components often proved to be untenable and utilized various forms of indexing or other flexible pricing for such components. In the current environment, with inflation and significant price volatility, suppliers (and OEMs) are rethinking the traditional structure for component contracts. Long-term contracts at a fixed, or even declining, price may no longer be practical. As has been the case in the past with raw material-intensive components, suppliers should focus (and wise OEMs will cooperate) in implementing greater pricing flexibility into their contracts to account for changing costs, whether through some form of defined indexing, a periodic opportunity to renegotiate and market test, or other creative approaches.
- Warehousing and inventory banks. For decades the traditional model in the automotive industry has been lean, just-in-time (JIT) inventory management, as suppliers and OEMs alike maintain only minimal levels of inventory. This is an incredibly efficient model — as long as everything is running smoothly and on-time. However, as the pandemic and supply chain issues have laid bare over the last two years, once all of the proverbial “fat” has been stripped out of the system, there is nothing left to cushion a blow. Suppliers and OEMs both must weigh the potential benefits of lean inventory against the risks posed by a supply chain that is far less stable and predictable than it was two years ago. Many companies have incurred significant costs for expedited freight, overtime, shutdowns, and other expenses that have far outstripped any savings and efficiencies realized from trying to maintain a lean inventory. As a result, OEMs and suppliers alike are looking at ways to mitigate these risks. In addition to looking at reshoring and shortening supply chains (which primarily are long-term strategies with little capacity for short-term relief), many companies are rethinking their inventory models and moving to implement warehousing and larger inventory banks as a shield against shortages and disruptions. While this approach can be an effective strategy, it is not without its own added costs. Suppliers must think carefully when implementing such a strategy (either on their own initiative or at the request of their customers) to ensure that the costs are properly apportioned and accounted for.
- Shifting risk for freight. For many suppliers, freight costs have taken on outsized significance over the course of the last two years, both due to increased need for expedited freight and rapidly increasing costs (and delays) for ordinary shipping. Traditionally the OEMs treated most shipping costs, including costs for expedited freight (even in cases of force majeure and commercial impracticability) and costs to ship components from lower-tier suppliers, as something for which their suppliers were responsible. However, many suppliers are questioning this structure and pushing back. Numerous suppliers have struggled with increased costs for shipping, particularly those needing to obtain components from Asia. As discussed above with respect to pricing and costs more generally, suppliers should look for ways in which to share some of the burdens and risks of these costs with their customers. Many suppliers also have struggled with a need for frequent (and for some periods, near-constant) expedited freight in order to compensate for delays in the supply chain. As most suppliers know, costs for expedited freight can rapidly become exorbitant and threaten to surpass a supplier’s profit margins on a program for an entire year or even longer. In recent years, suppliers and OEMs have treated costs for expedited freight as a zero-sum game, with OEMs demanding that their suppliers pay the entire costs for expedited orders and suppliers often balking and refusing to pay such costs (even if otherwise obligated to do so under the applicable contract/law). Given that the challenges in the supply chain show no sign of alleviation soon, companies should consider possible new approaches in which the suppliers and OEMs share some of the risk for expedited freight arising out of issues that are outside of their control.
IV. Strategies for Distressed Suppliers and Opportunities for Growth
While many suppliers will certainly forge a path forward, others will face demands from their customers for support in the form of price increases, acceleration of receivables, and even exit agreements and demands to find a new source of supply. This presents some possible additional costs for many suppliers, but it presents as well some possible acquisition opportunities for other suppliers who are looking to grow their business.
- Support for financially or operationally troubled suppliers. In many cases, suppliers seek to pass increased costs on to their customers, and the end-customer OEM often resists absorbing these increased costs. In cases where a customer provides financial or other support to a sub-tier supplier, the following terms help to protect each side so that parts can continue to flow through the supply chain:
- The supplier’s commitment to continue producing the parts for the customer;
- If applicable, the lender’s commitment to continue lending to the supplier so that it continues to operate and produce the parts for the customer;
- The customer’s commitment to continue paying, limit its right of setoff, and/or establish new payment terms;
- Establish milestones to gauge the supplier’s performance;
- Identify and acknowledge ownership of tooling;
- Where applicable, provide for the customer’s right to access the supplier’s facilities;
- Include provisions to help “preference-proof” the agreement in the event of a bankruptcy filing.
- Acquisition opportunities. As some automotive suppliers face financial or operational headwinds, investors (including some automotive suppliers) are also focused on opportunities to acquire promising businesses that may face near-term financial and operational challenges at lower valuations than were available prior to the pandemic. While these deals may appear to be hard to come by, shrewd investors will be well served by considering out-of-court acquisitions of distressed companies. For more information on the fundamental considerations to help guide investors to a successful deal, see deal, see “Possible Silver Lining: Targeted Acquisitions – Financial and Operational Distress in the Supply Chain Presents Opportunities for Growth” article on Page 30.
CONCLUSION | |
The global supply chain has changed and suppliers must adapt to the new circumstances. The challenges faced by suppliers in 2021 are likely to continue into 2022. If 2021 taught the industry anything, it is to expect the unexpected and apply the “lessons learned” to navigate challenges going forward. These challenges will require suppliers to reevaluate many of their contracting and operations, including their approach to managing the risks inherent in pricing, warehousing/inventory, and freight costs. More volatility in the supply chain requires that contracts be more flexible in order to allow for a bend-but-don’t-break approach to resolving challenges as they arise. |
2 https://ihsmarkit.com/research-analysis/fuel-for-thought-auto-demand-levels-remain-depressed-on-chip-famine.html
Essential Compliance Updates for Multinational Automotive Companies
AUTHORS | |||||
Greg Husisian | ghusisian@foley.com | |||||
John Turlais | jturlais@foley.com | |||||
Jenlain Scott | jcscott@foley.com |
Recent White House initiatives and speeches by Department of Justice officials (and the President himself) have emphasized the importance that the Biden Administration is putting on enforcement of international regulations, such as the Foreign Corrupt Practices Act (FCPA), export controls, and the economic sanctions overseen by the U.S. Treasury Department. Although these international regulations saw record fines under the Trump Administration, the billions of dollars of imposed penalties largely were confined to a few, high-profile enforcement actions. But all indications are that enforcement of international regulations will be broader and deeper in the new administration, putting all multinational automotive companies that operate, source from, or sell abroad on notice that they need to enhance compliance measures in these areas.
The opening salvo occurred in a June 2021 speech by President Biden. The President designated the fight against corruption as a core national security interest of the United States and directed members of his team to develop a Presidential strategy to support this initiative.1 By explicitly linking corruption with U.S. national security interests, the President elevated the rationales and importance of fighting corruption, from one of leveling the competitive playing field for companies that follow the law to one of national security imperative.
In accordance with this directive, the White House followed up with a December report, titled the U.S. Strategy on Countering Corruption.2 The strategy focuses on five main pillars:
- modernizing, coordinating, and resourcing U.S. Government efforts to fight corruption;
- curbing illicit finance;
- holding corrupt actors accountable;
- preserving and strengthening the multilateral anti-corruption architecture; and
- improving diplomatic engagement and leveraging foreign assistance resources to advance policy goals.
The administration has started to implement these goals. During the keynote address at the Global Investigations Review Connect: New York event, Principal Associate Deputy Attorney General John Carlin provided concrete examples of how the administration is taking action and augmenting resources to fight corruption.3 For the first time, there will be a FBI squad dedicated to DOJ’s Criminal Fraud Section, with a specific emphasis on investigating FCPA violations, commodities and securities fraud, cryptocurrency and financial institutions fraud, and health care fraud. PADAG Carlin further stated that the government will increase its current practice of using “big data” to identify and prosecute cases.
Importantly for multinational companies and companies that export U.S.-origin goods, PADAG Carlin also stated that the administration will emphasize economic sanctions and export control enforcement. He emphasized that the DOJ has broadened its view on what could be an export control violation, now including both transferring intellectual property and “human knowledge.” This expansive view of what constitutes controlled technical data represents a subtle but important change in the breadth of technical information that can support a deemed export violation. Because sanctions and export controls are both ways to protect national security and U.S. technology, PADAG Carlin’s speech aligns with President Biden’s approach of linking enforcement of international regulations with U.S. national security interests.
Along these lines, on October 28, 2021, Deputy Attorney General Lisa Monaco gave the keynote address at the ABA Conference on White Collar Crime.4 In her address, DAG Monaco emphasized four main points of key concern to multinational automotive companies.
Key Concerns for Multinational Automotive Companies
- DOJ Movement to a Holistic Review of a Corporation’s Entire Criminal, Civil and Regulatory History. DAG Monaco’s speech noted a clear shift in DOJ policy when it comes to reviewing a corporation’s violations and compliance history, emphasizing that the DOJ will consider all prior misconduct (and not simply “similar” prior misconduct) when making charging, penalty, and other decisions. This change can have particular relevance for multinational automotive companies, as it opens the door to considering charges of multiple legal regimes, even potentially including those of other countries. This policy shift could be especially relevant for automotive companies that operate in foreign, high-risk environments, such as China, Brazil, or Mexico, or that have regular exposure to multiple legal regimes, such as in the areas of export controls and economic sanctions.
- DOJ Continuing Emphasis on Knowing Specific Personnel Involvement. DAG Monaco also emphasized the importance of corporate entities being explicit and fulsome when it comes to identifying personnel involved in any enforcement action. Specifically, DAG Monaco emphasized that when cooperating with the government, companies must identify all individuals involved in the misconduct, regardless of their individual levels of involvement. DAG Monaco also indicated that the DOJ was restoring prior guidance that to be eligible for any cooperation credit, companies truly need to provide all non-privileged information about involved individuals, regardless of magnitude of involvement.
- DOJ Will Not Tilt the Scales Against Having Corporate Monitors. DAG Monaco explained that in recent years there has been guidance suggesting that corporate monitor-ships would be the exception and not the rule. She stated that the DOJ had rescinded that guidance and clarified the DOJ is free to require independent corporate monitorships whenever it deems appropriate.
- The DOJ Expects Companies to Actively Review their Compliance Programs to Monitor and Remediate Misconduct. Perhaps the most useful piece of DAG Monaco’s speech was her guidance surrounding compliance policies and why these are key consideration in charging and other enforcement decisions. While many of the new (or newly re-implemented) DOJ policies focus on the prior misconduct of companies or individuals, compliance programs are a way to prevent and preempt the misconduct in the first instance, as well as a way to signal to enforcement authorities that a company is and was taking compliance with the international regulations seriously. For automotive companies that operate in high-risk environments on multiple continents, the new emphasis on heightened compliance is an invitation to perform new risk assessments and evaluations of the efficacy of existing compliance measures.
The DOJ’s guidance on the importance of compliance programs is especially important for automotive companies that operate, source from, or sell abroad. For these companies, a fresh assessment of their export controls, economic sanctions, and export controls compliance policies and related internal controls, such as OFAC screening protocols and export controls technology control plans, is a prudent investment in compliance resources. In each case, the company should assess the current compliance program to see if its compliance measures and internal controls line up with its risk profile. In particular, the evaluation should consider whether the plan properly covers the following aspects of the company’s risk model.
Key Considerations for Companies to Assess Compliance Program
- Does your company’s relevant compliance program reflect all of the circumstances that may put the organization at risk of a violation? Is it based upon a realistic risk assessment that is up to date and consistent with the company’s current circumstances and current business and regulatory risk profiles?
- Does your company’s export controls, economic sanctions, and FCPA compliance programs cover all aspects of the business that operate, source from, or sell overseas?
- Do your export controls, economic sanctions, and FCPA compliance programs reflect the nature of the firm’s foreign business operations, including both direct operations and those that can create third-party liability, such as agents, consultants, or sales through distributors?
- Does each compliance program contain adequate internal controls to help buttress the compliance procedures, such as internal controls relating to gifts, meals, entertainment, and travel (FCPA/anticorruption), screening for specially designated or blocked persons (OFAC/economic sanctions), stop, hold, and release procedures (OFAC/economic sanctions and export controls), and a physical security/badging and technology control plan (for companies that deal with export-controlled goods or technical data)?
- Do the relevant compliance measures compare well with codes of ethics and compliance policies used by comparable businesses in the industry and in the countries where the firm operates?
- Has your company done an export controls classification review to determine whether it has correctly identified all controlled goods and technical data?
- Has your company correctly identified all compliance stakeholders and confirmed that they have received tailored training on all high-risk international regulations and compliance measures that are relevant to their work? Are training and compliance materials accessible and translated into local languages?
- Does your company provide adequate resources, means, and support for employees to report suspicious or improper conduct without fear of retaliation? If so, are these measures in place both in the United States and abroad?
- Does your company periodically test its compliance processes and procedures to ensure that they are being implemented properly at the operational level and that they are effectively addressing risks based on the company’s actual business practices?
If your organization has not conducted an international regulatory risk assessment or reviewed its compliance measures over the last three years, the recent announcements and initiatives by the Biden administration are a good reminder that such compliance steps are overdue. Because multinational automotive companies often operate in or source from high-risk countries, such as China and Mexico, it is especially important for automotive companies to take a fresh look at their compliance measures to ensure that they are meeting the expectations of regulators and are adequately protecting the company’s interests in complying with the complicated laws that govern international conduct and exports.
1 See Memorandum on Establish the Fight Against Corruption as a Core United States National Security Interest (June 3, 2021) (available at: https://www.whitehouse.gov/briefing-room/presidential-actions/2021/06/03/memorandum-on-establishing-the-fight-against-corruption-as-a-core-united-states-national-security-interest/).
2See United States Strategy on Countering Corruption (December 6, 2021) (available at https://www.whitehouse.gov/briefing-room/statements-releases/2021/12/06/fact-sheet-u-s-strategy-on-countering-corruption/.)
3 See John Carlin on Stepping Up DOJ Corporate Enforcement (speech given on October 5, 2021) (available at https://globalinvestigationsreview.com/news-and-features/in-house/2020/article/john-carlin-stepping-doj-corporate-enforcement.)
4See Deputy Attorney General Lisa O. Monaco Gives Keynote Address at ABA’s 36th National Institute on White Collar Crime (October 28, 2021) (available at https://www.justice.gov/opa/speech/deputy-attorney-general-lisa-o-monaco-gives-keynote-address-abas-36th-national-institute.)
NHTSA and Motor Vehicle Safety – 2022 Developments
AUTHORS | |||||
Christopher Grigorian | cgrigorian@foley.com | |||||
Nicholas Englund | nenglund@foley.com |
The National Highway Traffic Safety Administration (NHTSA or the Agency), the nation’s primary regulator of vehicle safety, will likely be increasingly active in 2022 as the Biden Administration’s enforcement philosophy and priorities have come into finer focus over the past year. NHTSA has been leveraging regular, voluntary meetings with manufacturers both to learn more about emerging technologies and identify potential field issues involving the manufacturer’s products in advance of a determination by the Agency to open a formal investigation. In addition to a broader flexing of its enforcement powers, NHTSA also has been aggressively using its information-gathering tools to inform its priorities. Notably, the Agency listed a full slate of rulemakings in the current (Fall 2021) U.S. Department of Transportation’s Unified Regulatory Agenda. This full regulatory agenda will only be further expanded by several legislative mandates contained in the recently passed Infrastructure Investment and Jobs Act (2021 Infrastructure Act).
NHTSA’s approach to enforcement under the Biden Administration.
Over the past year, NHTSA has taken a much more aggressive approach in using its information gathering powers and informal requests for information to identify and evaluate issues related to vehicle safety. This more aggressive approach is reflected in a number of Agency actions, including the Agency’s expanded use of standing general orders, informal meetings with manufacturers, and information requests to peer manufacturers and suppliers to support ongoing investigations.
In 2015, as part of its air bag inflator investigation, NHTSA issued standing general orders to monitor field events. In 2021, NHTSA extended the use of standing general orders to monitor field events involving Automated Driving Systems (ADS) and Level 2 Advanced Driver Assistance Systems (ADAS) under Standing General Order (SGO) 2021-01. Like prior standing general orders, SGO 2021-01 requires manufacturers to submit detailed information regarding field incidents on an ongoing basis. But unlike prior standing general orders, NHTSA did not initiate SGO 2021-01 in conjunction with an open investigation, and it extended the order to vehicle operators (non-manufacturers). In addition, the reporting requirements specifically seek details on crashes involving “vulnerable road users,” which include pedestrians, persons traveling in wheelchairs, bicyclists, motorcyclists, and riders or occupants of other transportation vehicles that are not motor vehicles, such as all-terrain vehicles and tractors.
The order was issued to more than 100 manufacturers and operators and requires them to submit reports if they receive notice of certain crashes involving an ADS or Level 2 ADAS-equipped vehicle that occur on publicly accessible roads in the United States. NHTSA further requires the reporting entities to submit a “null report” for each month in which the entity did not otherwise report an incident to NHTSA. Underscoring the Biden Administration’s support of this aggressive approach, the Agency sought and received “emergency” clearance from the Office of Information and Regulatory Affairs, part of the Office of Management and Budget, under the Paperwork Reduction Act, for this information collection.
The Agency has also continued requesting recurring, informal meetings with vehicle manufacturers and certain Tier 1 suppliers. In these meetings, personnel in NHTSA’s Office of Defects Investigation discuss Vehicle Owner Questionnaires – complaints sent directly to the Agency – and issues under review within the manufacturers’ safety offices.
Another trend is NHTSA’s increased use of peer manufacturer and supplier information requests during formal defect investigations, especially in connection with investigations involving newer and emerging technologies.
In recent years, NHTSA has automated many of its tools for auditing the recall-related documents manufacturers are required to submit to the Agency. NHTSA has continued using these automated audits to check the completeness of recall files and to alert manufacturers when information is missing or deadlines have been missed. The Agency has begun to include alerts related to potentially missing information identified in its recall acknowledgment letters.
In terms of civil penalties, NHTSA negotiated a significant penalty with a vehicle manufacturer, as well as penalties against several registered importers during 2021. In August 2021, the Agency announced that it had negotiated a settlement with Piaggio for a total of $750,000 related to allegations of untimely recalls, quarterly recall reports, and submissions of manufacturer communications under 49 CFR 579.5. The violations reflect NHTSA’s increased scrutiny of the timeliness of all filings made by a manufacturer.
The Agency also penalized five registered importers for importation and certification violations. Three of the registered importers had their registrations suspended for various violations of the regulations related to importing gray market vehicles. Another registered importer consented to a $500,000 civil penalty and had its registration suspended for 125 days. NHTSA held $300,000 of the penalty in abeyance; if the importer commits additional violations, the remaining penalty will become due and its registration will be revoked. A fifth registered importer entered a consent order, agreeing to a $30,000 civil penalty and a 150-day suspension. NHTSA is holding $20,000 of the civil penalty in abeyance for a year, which it will waive, if the importer has no additional violations during that time.
NHTSA has a full rulemaking schedule for 2022
As expected, the Biden Administration’s focus on environmental issues led NHTSA to begin the process of amending the corporate average fuel economy standards. Also, NHTSA closed 2021 by finalizing NHTSA’s proposal to repeal in full “The Safer Affordable Fuel-Efficient (SAFE) Vehicles Rule Part One: One National Program,” published on September 27, 2019, in which NHTSA codified regulatory text and made additional pronouncements regarding the preemption of state and local laws related to fuel economy standards. The repeal marks a significant break from the prior administration.
On December 29, 2021, NHTSA published a final rule establishing FMVSS 227, Bus rollover structural integrity. The new safety standard applies to “over-the-road buses” and buses that have a gross vehicle weight rating (GVWR) greater than 26,000 pounds. The final rule fulfills the Congressional mandate from the Moving Ahead for Progress in the 21st Century Act (MAP-21) of 2012. This long-overdue final rule may indicate that the Agency will prioritize finalizing some of the other rulemakings required by MAP-21 and the Fixing America’s Surface Transportation (FAST) Act of 2015.
The Agency has also publicly announced an ambitious rulemaking agenda. The Unified Regulatory Agenda for the U.S. Department of Transportation issued in the Fall of 2021 sets forth a slate of upcoming rulemakings for NHTSA, including:
- An Advanced Notice of Proposed Rulemaking (ANPRM) seeking public comments on modernizing FMVSS 108, Lamps, reflective devices, and associated equipment, to facilitate new designs and emerging technologies.
- An ANPRM seeking public comments on amending the rear visibility standards in FMVSS 111 to permit cameras to replace rearview mirrors.
- A Notice of Proposed Rulemaking (NPRM) amending the record retention requirements to reflect requirements in the FAST Act of 2015.
- An NPRM to amend Part 577, Defect and Noncompliance Notification, to permit electronic notification in addition to notice by first class mail, as allowed by MAP-21.
- An NPRM seeking comments on requiring automatic emergency braking (AEB).
- An NPRM to upgrade the motorcycle helmet requirements.
- An NPRM that would extend the electrolyte spillage requirements of FMVSS 305 to vehicles with a gross vehicle weight rating (GVWR) of 10,000 pounds or more.
- A final rule to upgrade the rear impact guard requirements for trailers and semitrailers.
- A final rule that addresses the crashworthiness regulations that may be necessary to facilitate the certification of new vehicle designs equipped without driver controls.
While several of these items were previously delayed, many of the target dates in this recently published regulatory agenda will fall during 2022. Notably, the recent passage of the Infrastructure Investment and Jobs Act of 2021 (Infrastructure Act) reflects Congress’s intent to accelerate the completion of long-delayed rulemakings that continue to be reflected in the Agency’s regulatory agenda.
The Infrastructure Investment and Jobs Act of 2021 includes provisions aimed at motor vehicle safety
On November 15, 2021, President Biden signed the Infrastructure Act into law. Many of the Infrastructure Act’s provisions impose rulemaking mandates upon NHTSA, reflecting Congress’s interest in proactively influencing NHTSA’s enforcement and regulatory priorities. Most importantly, the Infrastructure Act provides new funding to the Agency through the Highway Trust Fund, which currently funds some of NHTSA’s activities. It also provides grant funds for states to modernize their data collection systems to enable full electronic transfer of crash data to NHTSA and directs NHTSA to upgrade its systems to support states’ efforts to modernize their data collection systems. The data collected through these grants comprise NHTSA’s Fatal Accident Reporting System and the Crash Investigation Sampling System. As part of the funding, Congress directed NHTSA to revise the crash data elements it collects in order to distinguish “individual personal conveyance vehicles, such as electronic scooters and bicycles, from other vehicles involved in a crash” and to collect data elements “relating to vulnerable road user safety.” Infrastructure Act § 24108(a), (c). The focus on vulnerable road users echoes NHTSA’s requirements under Standing General Order 2021-01 requiring manufacturers to report incidents involving both automated technologies and vulnerable road users. Similarly, Congress provided additional funding in the Infrastructure Act to expand NHTSA’s Crash Investigation Sampling System to collect data on “all crash types” and to add on-scene investigation protocols.
In addition to providing data to determine the number of fatal accidents on public roads, the data fields also require the reporting entity to provide information detailing certain attributes related to the reported crashes, such as whether the airbag deployed. Manufacturers should monitor this modernization process, as the Agency has spent the past decade developing additional data-analytics tools. These tools are part of a relational database to tie together the various data streams NHTSA receives (such as VIN deciphering information, early warning reports, responses to information requests and standing general orders, and recall data). The Agency intends to use analytics to identify and evaluate defect trends that may otherwise be missed. Moreover, portions of the Infrastructure Act may facilitate making more of this data publicly available.
The 2021 Infrastructure Act also includes the following specific directives to NHTSA:
- § 24111, Motorcycle Advisory Council, requires the U.S. DOT to establish the Motorcyclist Advisory Council to evaluate motorcycle safety, barrier and road design, and the potential implementation of intelligent transportation systems.
- § 24202, Recall Completion Reports, extends the quarterly recall completion reports in 49 CFR 573.7 from six consecutive quarters to eight consecutive quarters, and requires manufacturers to submit annual reports “for each of the three years beginning after the date of completion of the last quarter for which a quarterly report is submitted.”
- § 24204, Seat Back Safety Standard, directs NHTSA to issue an advanced notice of proposed rulemaking within two years to update FMVSS 207, Seating systems.
- § 24205, Automatic shutoff, requires NHTSA to issue a final rule within two years requiring certain vehicles with keyless ignitions to be equipped with a system to automatically shut off the engine to avoid carbon monoxide poisoning.
- § 24208, Crash Avoidance Technology, directs NHTSA to promulgate crash avoidance safety standards that would require all passenger vehicles to be equipped with forward collision warning, automatic emergency braking (AEB), lane departure warning, and lane keeping assist systems. Congress did not put a deadline on these requirements.
- § 24209, Reduction of Driver Distraction, requires NHTSA to research and report to Congress regarding the installation and use of driver monitor systems to “minimize or eliminate” driver distraction, driver disengagement, “automation complacency” by drivers, and foreseeable misuse of ADAS technologies. Congress does not necessarily require NHTSA to promulgate rulemaking. If, based on the report, NHTSA determines that rulemaking is “necessary to ensure safety,” it must promulgate rulemakings within two years of completing the report to Congress.
- § 24210, Rulemaking Report, requires NHTSA to report to Congress within 180 days on several rulemakings required by prior legislation, including the MAP-21 and FAST Act, as well as any rulemaking required by the Infrastructure Act.
- § 24212, Headlamps, requires NHTSA to finalize the Adaptive Driving Beam rule within two years.
- § 24213, New Car Assessment Program, requires NHTSA to finalize within one year the Agency’s 2015 NPRM that proposed providing consumer information on several crash-avoidance technologies.
- § 24214, Hood and Bumper Standards, requires NHTSA to publish a notice for public comment regarding potential updates to hood and bumper standards that considers (1) advance crash-avoidance technologies, (2) technologies that would “reduce the number of injuries and fatalities suffered by pedestrians, bicyclists, and other vulnerable road users,” and (3) potential harmonization with United Nations Economic Commission for Europe Regulation Number 24 (UNECE R24).
- § 24216, Early Warning Reporting (EWR), amends the EWR requirements by stating that manufacturers shall comply with any EWR requirements notwithstanding any order entered in a civil action restricting disclosure of information.
- § 24217, Improved Vehicle Safety Databases, requires NHTSA to improve public accessibility to publicly available information obtained by the Agency. Congress specifically directs NHTSA to ensure that the Agency make publicly available nonconfidential documents and materials relating to information created or obtained by the Agency “in a manner that is (A) timely; and (B) searchable in databases by any element that the Secretary [delegated to NHTSA] determines to be in the public interest.”
- § 24220, Advance Impaired Driving Technology, requires NHTSA to issue a final rule requiring new passenger vehicles to be equipped with “advanced drunk and impaired driving prevention technologies” within two years.
- § 24222, Child Safety, directs NHTSA to issue a final rule within two years requiring all vehicles with a gross vehicle weight rating (GVWR) less than 10,000 pounds to be equipped with a rear-seat alert after deactivating the engine.
While many of these Congressional directives will require NHTSA to promulgate or finalize existing proposed rules, the requirement to provide two additional quarterly reports and three annual reports covering recall completion rates and the changes to the EWR statutory language have already gone into effect and do not require further rulemakings by NHTSA.
NHTSA’s robust enforcement program and extensive regulatory agenda will certainly present challenges for the automotive industry throughout 2022. To reduce enforcement risk, manufacturers must ensure that their internal safety evaluation and reporting procedures are up-to-date and that key personnel are properly trained to identify and escalate potential safety defects and other potentially reportable events. These procedures should also include a process for confirming that all filings are timely and complete, and that amendments or updates to reports are timely submitted. Manufacturers should also have processes in place to monitor regulatory developments and, where appropriate, participate in the rulemaking process by submitting comments and/or engaging with their industry associations to ensure that the Agency’s rulemakings reflect input from all stakeholders.
2022 Antitrust Outlook – Significant Changes Under the Biden Administration
AUTHOR | |||||
Greg Neppl | gneppl@foley.com |
The Biden Administration is pursuing aggressive antitrust law enforcement. This article identifies some issues to watch.
On July 9, 2021, President Biden issued an executive order on “Promoting Competition in the American Economy.” While directed at various federal agencies and departments, the order specifically calls for “vigorous” antitrust enforcement by our two federal antitrust agencies, the Department of Justice (Antitrust Division) (DOJ) and the Federal Trade Commission (FTC). While historically U.S. antitrust enforcement has been marked more by continuity than abrupt change, we are now seeing shifts in agency direction that could affect many businesses and industries, including the automotive industry. These shifts may be particularly relevant to the evolution of the automotive industry, as huge investments are being made to develop and manufacture electric vehicles and related battery technologies.
2022 M&A Related Developments
Merger and acquisition activities are often high in industries undergoing transformation, as established firms seek to develop innovative products, establish new supply chains (or make vertical acquisitions of vendors and suppliers), and invest in or acquire technologies to position themselves to compete with each other as well as with new entrants (often funded by venture capital).
How the antitrust agencies will approach M&A activity in the automotive industry — a technology industry as much as a manufacturing industry — could be influenced by the many antitrust changes proposed (or already imposed) under the Biden Administration. These topics include:
- Possible Changes to the Horizontal and Vertical Merger Guidelines: President Biden’s executive order on promoting competition called on the FTC and DOJ to “review the horizontal and vertical merger guidelines and consider whether to revise those guidelines.” A subsequent FTC/DOJ press release, dated July 9, 2021, stated that the “current guidelines deserve a hard look to determine whether they are overly permissive.” Speculation abounds as to how the agencies might seek to revise these guidelines. Market share caps, the elimination of the Herfindahl-Hirschman Index (HHI) as a measure of market concentration, and applying a “public welfare” standard (in place of the long-established “consumer welfare” standard) as the antitrust guidepost for identifying anticompetitive mergers have all been proffered by commentators. Some advocates have argued that a “public welfare” standard should include consideration of a wide range of issues, such as effects on labor, environmental concerns, racial impacts, and wealth inequality concerns. The FTC has reportedly requested information in merger reviews on topics like unionization, equity, franchising, and environmental, social, and governance issues, which would appear unrelated to traditional antitrust considerations and the “substantially lessen competition” standard for merger challenges set forth by statute in Section 7 of the Clayton Act.
Such an expansion of the cognizable issues relevant to merger reviews could substantially alter the predictability of agency merger enforcement efforts. Such revisions, if made — or even if applied by the antitrust agencies informally, as an exercise in agency “enforcement discretion” — could mark a change in merger enforcement, with impacts on strategic planning, business confidence, and business valuations.
- Vertical Merger Guidelines Withdrawn by the FTC: In September 2021, the FTC voted unilaterally to withdraw its approval of the Vertical Merger Guidelines, adopted jointly by the FTC and DOJ in June 2020. (To date, DOJ has not similarly withdrawn its approval of those guidelines.) The utility of this agency enforcement guidance to businesses and the antitrust bar is therefore in question, at least in transactions pending FTC review.
- FTC “Informal Interpretations” of HSR Rules are Under Review. For decades the FTC’s Premerger Notification Office (PNO) has provided regular informal guidance to the antitrust bar on interpreting and applying the merger notification rules set forth in the Hart-Scott-Rodino Antitrust Improvements Act of 1976 (HSR) and implementing regulations. In a blog post dated August 26, 2021, however, the FTC’s Bureau of Competition stated a concern that these “informal interpretations may not reflect modern market realities or the policy position of the Commission.” While HSR informal guidance is still available, the blog post noted that the FTC is “currently in the process of reviewing the voluminous log of informal interpretations to determine the best path forward.”
- FTC “Warning Letters”: The FTC announced in August 2021 that it may send letters to parties to transactions under FTC investigation stating that, despite imminent expiration of the HSR waiting period, the FTC investigation remains open, and if the parties choose to close the transaction, they are “doing so at their own risk.” The legal significance of such a warning letter in any subsequent FTC challenge to a consummated transaction has yet to be tested. At a minimum, however, such letters may inject deal uncertainty by potentially delaying closings and extending the timeframe for deal reviews beyond the statutory waiting period established by the HSR Act.
- Antitrust Concerns with “Technology” Acquisitions: President Biden’s executive order on promoting competition cited “dominant tech firms” as “undermining competition and reducing innovation” through “killer acquisitions,” including the acquisition of “nascent competitors.” While primarily focused on technology acquisitions by “Big Tech” platforms, this technology acquisition concern could apply to other industries. As the automotive industry transitions to new power and drive train solutions, technology acquisitions in the automotive industry could receive greater agency scrutiny.
2022 Additional Developments
Changes under the Biden Administration extend beyond M&A. Some of these include:
- Antitrust Concerns with “Labor Markets”: The automotive industry is labor intensive, and the Biden Administration has signaled that “labor markets” are a topic of high antitrust interest. The FTC and DOJ have recently held a number of workshops addressing competition issues affecting labor markets and the welfare of workers. Topics discussed included labor monopsony; the use of restrictive clauses in labor agreements, including non-competes and non-disclosure agreements; information sharing and benchmarking activity among competing employers; and the relationship between antitrust law and collective bargaining efforts in the “gig economy.” Employee non-competes were a particular focus of these workshops.DOJ has (even prior to the Biden Administration) pursued companies engaged in employee “no-poach” agreements, sometimes as a criminal antitrust violation. Automotive industry firms will want to follow Biden Administration labor policy changes, including the possible use of antitrust law to effectuate policy changes.
- Antitrust Interest in Supply Chain Disruptions: Automotive industry supply chains are complex. On November 29, 2021, the FTC voted to conduct a study of whether and how the supply chain interruptions of the past year have affected competition. The study will look to answer two central questions that may be of interest to manufacturers: (i) why these disruptions occurred and (ii) whether they are leading to specific “bottlenecks, shortages, anticompetitive practices or contributing to rising consumer prices.” According to the FTC announcement, an order for detailed information will be sent to nine large retailers, wholesalers, and consumer good suppliers in the United States. That said, the FTC certainly could expand this probe to include other companies, including manufacturers in a supply chain or other industries.
- Authorizations for FTC Antitrust Investigations: In July and September 2021, the FTC — through some 15 resolutions — authorized compulsory process for FTC investigations over a wide range of antitrust topics, including proposed and consummated mergers, suspected monopolization, and suspected abuse of intellectual property. Under these resolutions, a single FTC commissioner may authorize FTC staff attorneys to issue compulsory process (such as civil investigative demands and subpoenas). Previously, such prior delegations applied virtually only to consumer protection investigations, as opposed to antitrust investigations.
With full Commission oversight of antitrust investigations rescinded, there may be “less accountability and more room for mistakes, overreach, cost overruns, and even politically-motivated decision making,” according to FTC Commissioners Phillips and Wilson in their dissenting statement of September 14, 2021. Whether and how this lowering of the threshold for the FTC to launch antitrust investigations could affect automotive industry participants is unknown, but it does reflect a change worth considering. As both the FTC and DOJ have authority to review and challenge consummated deals — even deals that were notified and received HSR clearance — one possible outcome of these resolutions is to increase the number of investigations of consummated transactions.
The Continuing Risks from Cartel Conduct
The developments discussed above are largely driven by the Biden Administration, although one antitrust risk that transcends administration changes and partisan lines is cartel conduct. We cannot forget the lessons of DOJ’s long-running investigation of auto parts suppliers, one of the largest criminal investigations ever pursued by its Antitrust Division, which resulted in charges against some 48 companies and yielded almost $3 billion in criminal fines. Settlements of class action and other private plaintiff claims reportedly exceeded $1 billion.
While DOJ’s Antitrust Division has long pursued both companies and individuals criminally in cartel cases, the Biden Administration’s Deputy Attorney General Lisa Monaco announced in October 2021 that DOJ would enhance efforts to charge individuals in white-collar prosecutions. You may recall the famous “Yates memo” from 2015 — issued by then Deputy Attorney General Sally Yates — announcing stepped-up efforts to prosecute individuals. The October 2021 announcement appears to renew and reinvigorate this focus on prosecuting individuals.
Automotive industry participants may have little control over Biden Administration-initiated changes to the merger and non-merger enforcement policies discussed above. An effective antitrust compliance program, however, can pay real dividends by detecting and deterring cartel conduct. Though DOJ historically did not give credit for antitrust compliance programs in making charging decisions and sentencing recommendations, it announced changes to both policies in July 2019. These changes increase the legal benefits of implementing an effective antitrust compliance program.
Nearshoring Trends and Important Considerations When Looking to Mexico
AUTHORS | |||||
Vanessa Miller | vmiller@foley.com | |||||
Alejandro Gomez | agomez@foley.com | |||||
Fernando Camarena | fcamarena@foley.com |
Nearshoring refers to the transfer of certain business operations to a “nearby” country in preference to a more distant one. This article will explain the nearshoring trends and important considerations when looking to Mexico.
Nearshoring Benefits
Mexico boasts a number of proven advantages for companies looking to nearshore certain operations. Mexico is a nearshore prime manufacturing location with benefits across shipping, logistics, and labor — areas where many automotive companies are experiencing pain points in other manufacturing locales. Products originating from Mexico have preferential tariff access to the world’s largest markets, and its trade facilitation programs have been benefitting manufacturers for years.
Whether spurred by a long-term strategic plan or from lessons learned during the COVID pandemic, there is an increased focus on supply chain, and many companies are looking to revamp their supply chain and operational footprint. Global supply chains are already being transformed under the following principles: (i) resilient (secure, redundant, diverse) supply chains is the new name of the game; (ii) alternate purveyors will be preapproved, over a race to the bottom; (iii) provider adaptability will be favored over lean inventories; and (iv) increased transparency and preventive stress testing regarding purchaser’s needs and the supplier’s ability to fulfill them1.
Nearshoring Challenges
Despite the increased attention on supply chain issues and the operational headaches that manufacturers are facing, companies may be hesitant to overhaul their existing supply chain footprint or may not consider the long-term benefits of undertaking a more moderate nearshoring effort. Changing the supply base is extremely complicated. Supply chains are built on economic efficiencies, with many important inputs anchored in other faraway locations and companies committed to long-term contracts. However, there are a number of mounting pressures — including price increases, supply chain shortages, labor issues, and freight increases — that are converging to make automotive companies reassess the viability of their existing supply base and operations.
Companies that are considering nearshoring into Mexico immediately face the challenge of having to choose the most appropriate trade facilitation program to achieve the principles outlined above.
Even though a Maquiladora is usually chosen, this program is actually the most complex, burdensome, and risk-filled of those available2. In addition to the maquila program (now IMMEX for Manufacturing, Maquila, and Export Services Industries Program), there are a number of trade facilitation programs with varying degrees of complexity, namely, the Sectorial Promotion Program (PROSEC), Eighth Rule Permit, Refund of Import Duties to Exporters (Drawback), Inspection at Origin (Clearance Registry), and Integral Companies Certification Scheme (Certified Companies Registry).
Even though each company should carefully evaluate the proper model for their planned Mexico manufacturing operations, the following items should always be top of mind when conducting such an evaluation: (i) greater control over supply chains (shorter) and operations (closer), (ii) import duties, (iii) overall taxation (iv) Value Added Tax, (v) antidumping duties, and (vi) mandatory technical standards.
1. Shorter and Closer Product Inputs and Operations
Shorter supply chains reduce risk. Additionally, operations that are closer in proximity ensure greater access and oversight. Minimizing the distance and opportunities for shipping delays, logistical problems, etc., also lessens the number of issues that can be encountered and allows a manufacturer to react more quickly when there are complications.
2. Import Duties
Temporary importation of goods into Mexico is subject to payment of import duties, to the extent that the end products are exported to a relevant Free Trade Agreement country, most importantly due to market attractiveness those in the USMCA, the European Union, and the European Free Trade Association3.
There is a means to receive a refund for the lesser of the inputs’ import duties or those of the resulting products.
3. Overall Taxation
While nearshoring into Mexico, companies or investors can benefit from the important network of treaties signed with more than 60 nations to avoid double taxation. Provided that they are applied correctly, such treaties could yield advantages to repatriate profits and to reduce the overall tax exposure in Mexico. The current corporate income tax rate in Mexico is 30%, which could be seen as high in comparison to other countries. (Note that there is no local or state income tax on corporate earnings.) However, IMMEX manufacturing facilities can benefit from safe-harbor tax rules that could yield tax savings because the aforementioned rules often mean diminished manufacturing tolling fees to be paid for the Mexican facility, which in most cases is the main, if not the only, source of revenue for the Mexican operation.
Deciding the corporate structure of Mexican operations is quite relevant. For example, (i) a Limited Liability Company may confer tax benefits in the U.S., provided a number of requirements are met; (ii) a Stock Corporation could offer more flexibility from a legal corporate perspective for the shareholders; or (iii) a branch has the disadvantage that the parent company would be directly responsible of all its liabilities.
4. Value Added Tax (VAT)
Goods that are temporarily imported to Mexico for processing are subject to the payment of Value Added Tax, yet qualifying companies that obtain a VAT Certification benefit from fiscal credits in the exact same amounts of such tax. Alternatively, posting a bond or letter of credit may also avoid this levy.
5. Antidumping Duties4
Temporary imports into Mexico would be subject to antidumping duties exclusively when the corresponding Final Determination expressly determines that they are included in their scope. It is important and recommended that the Mexican Diario Oficial be researched.
6. Mandatory Technical Standards5
Until late 2020, the importation of inputs to be utilized in production processes, or of products that would not be sold to the public in the same shape or form as imported, were permitted to enter without proof of Norma Oficial Mexicana (NOM) compliance under “exemption letters.” As of today, importers must comply with all relevant NOMs, either prior to importation through duly certified compliance evaluations or after the importation process, using an existing contractual obligation with an authorized verifier to finalize such process within forty (40) days.
Even though virtually all for-export manufacturing makes use of at least one of the mentioned trade-facilitation programs, careful analysis of each is necessary to ensure appropriateness for each individual operation. How each program interacts with the items we have briefly described should always play a critical role in such an evaluation.
After all pros & cons have been weighed, it is hard to ignore (i) that Mexico enjoys access certainty to the USMCA region, (ii) that Mexico represents the lowest-cost option within the region, (iii) that delivery lead-times and logistics are hard to match by any other country in the world; and (iv) that USMCA grants Mexican exports favorable treatment regarding trade remedies and U.S. national security measures.
———————————————————-
1 See Foley & Lardner, LLP, Global Supply Chain Disruption and Future Strategies Survey Report (September 2020).
2 The terms “maquila” and “IMMEX” are often thought to correspond to two different programs, yet they are the same, with maquila being the original name that was later officially substituted with IMMEX. All of the original maquila permits, some of which are still functioning, have automatically been transformed into IMMEX permits.
3 The European Free Trade Association members are Switzerland, Norway, Liechtenstein, and Iceland.
4 Antidumping duties are determined on a country-by-country basis after an investigation concludes that specific unfairly traded imports caused damage to the relevant domestic industry.
/a>5 NOM is the name of the official, compulsory standards and regulations for diverse goods, products, and services in Mexico that may affect or represent a risk to the physical integrity and health of consumers, well-being of laborers in the workplaces, food safety, the environment, and other legitimate policy objectives.
Key Employment Issues Facing Employers in the Automotive Industry in 2022
AUTHORS | |||||
Jeff Kopp | jkopp@foley.com | |||||
Felicia O’Connor | foconnor@foley.com | |||||
Dan Kaplan | dkaplan@foley.com |
2022 is off to an interesting start on the labor and employment front in the automotive industry. As the COVID pandemic continues, employers continue to face a changing and complex landscape with respect to challenges related to continued remote work, labor shortages, and COVID protocol related accommodation requests. However, COVID matters will not be the only key issues facing employers in the automotive industry this year. Changes to the National Labor Relations Board (NLRB or Board) and its general counsel in 2021 mean that unionized and non-unionized employers will face challenges in the traditional labor arena as well. This section will explain the current state of the various vaccine mandates as well as some of the expected changes to NLRB precedent that are likely to affect employers in the automotive industry this year and beyond.
I. COVID, COVID, COVID – Even As the Pandemic Appears to Slow, Employment Related Challenges Remain
a. Remote Workforce Issues
Through the surges and slowdowns of COVID cases during the course of the pandemic, one pandemic related change seems here to stay. Greater number of workers are working remotely. While some businesses are encouraging workers to come back to the office, others have eased their remote work policies and face the challenges that come with a fully or partially remote workforce. Employers should take care to consider the legal implications of this change. If an employer now has employees working remotely in states where it previously did not have operations, there may be tax and other implications. Generally, the laws of the state where an employee works will govern the employee’s employment. If employees are working in a new state or locality, employers should make sure they are up to date on and mindful of those state and local laws that may differ from other locations where the employer operates. Are there local sick leave laws? Requirements for reimbursement of expenses? Careful consideration of local employment laws and regulations can prevent costly missteps.
b. Labor Shortage Pain – Difficulties in Hiring and Retention
Many employers are also currently facing an extreme labor shortage that has not only impacted hiring, but also retention of employees. In order to entice applicants and encourage employees to remain with the company, many employers have increased financial and other incentives. Signing bonuses, attendance bonuses, and other financial incentives can be an effective means to recruit and retain talent. In doing so, employers should be knowledgeable of the various wage and hour requirements in order to avoid any risk of unpaid wage or other claims. Employers should carefully consider whether the incentives they implement should be factored into the regular rate when calculating overtime. Likewise, employers should ensure that such incentives are consistently and fairly implemented.
c. Accommodation Requests for COVID Protocols
Since the outset of the pandemic, employers have had to contend with various requests for accommodation relating to COVID protocols whether related to mask or vaccine mandates, or leave issues. As an initial matter, employers should be aware that COVID can be a disability under the ADA depending on the employee’s symptoms. If an employee requests leave for COVID related symptoms, beyond what is typically granted by company policy, employers should involve legal counsel to determine on a case by case basis whether it may be considered a disability that would require the company to engage in the interactive process.
Even if an employee does not test positive for COVID, employers may receive requests for accommodation due to a disability or religion that prohibits the employees from complying with COVID related protocols. Many employers are familiar with this issue if they have a mask policy or vaccine policy. Employers should engage in the interactive process in such cases, in order to determine whether a reasonable accommodation can be granted which does not impose an undue burden on the company.
II. Changes to NLRB Standards and Priorities
COVID-related matters are not the only key issues facing employers in the automotive industry in the coming year. We have already seen some course corrections from the Trump-era labor board. As such, changes to NLRB standards and priorities will continue to affect unionized and non-unionized employers through 2022.
On July 22, 2021, NLRB General Counsel Jennifer Abruzzo issued her first memo, which set her agenda and priorities for her four-year term. In addition, with various terms expiring and resultant Democratic nominations submitted for consideration, the Board itself has also changed from a Republican to a Democratic majority, led by Chairman Lauren McFerran. Not surprisingly, the memo and Democratic majority on the Board mark a significant change in priorities from the Trump-era NLRB to a more union- and employee-friendly stance. The following potential changes in standards and priorities of the NLRB are anticipated:
a. Closer Scrutiny Regarding Employee Handbooks
The NLRB is likely to increase scrutiny of employee handbook provisions that may be construed to restrict activities protected under Section 7 of the National Labor Relations Act (NLRA). Under the Trump-era Board, the NLRB had adopted the Boeing test with respect to employee handbooks. This test assessed a facially neutral handbook policy by balancing the alleged restrictions against the employer’s legitimate justifications for implementing the policy. The test was much more flexible and employer-friendly than the previous standard under the Lutheran Heritage case, which prohibited any handbook policy, including those that did not explicitly prohibit protected activities, if the rule could be “reasonably construed” by an employee to restrict such activities. At the time, the Board viewed such rules to have a chilling effect on protected activities and thus considered them a violation of the NLRA. The Boeing case is specifically referenced in the general counsel’s August 12, 2021 memo as a case “involving board doctrinal shifts,” which upended prior precedent that “struck an appropriate balance between the rights of workers and the obligations of unions and employers.” This shows that the general counsel, and very likely the Board, are poised to return to the more employee-friendly Lutheran Heritage precedent. In anticipation of this change, employers should review their handbooks for possibly problematic policies and be ready to change such policies if the Board issues a decision overruling the employer-friendly Boeing standard.
b. Possible Increased Application of Weingarten Rights
As unionized employers know, Weingarten rights are the rights of represented employees to have union representation present when requested at an investigatory interview that may lead to discipline. Under current Board precedent, Weingarten rights only exist in a union environment. Specifically in 2017, the Board declined to extend Weingarten rights to an employee who was not represented by a union, but who had requested to have a co-worker present during a disciplinary interview. Over the years, the Board has changed its position on a few occasions regarding whether non-union employees have the right to request representation during investigatory interviews. In 2000, the Board had held that non-union employees did have a right to such representation but then changed its stance in 2004. The general counsel memo references the current Board precedent, which does not extend the right to non-union employees, as an “area or initiative” bearing reexamination. Employers should watch for Board changes in this area and make sure its human resources employees, and others conducting such interviews, are up to date on any changes with respect to whether non-union employees are entitled to representation upon request.
c. Access to Employer Property for Unionizing Purposes
Another area where non-unionized employers should be aware of potential change in Board precedent is with respect to union organizers’ access to, and use of, the employer’s property. Under the current state of the law, pursuant to Tobin Center for the Performing Arts, an employer is permitted to exclude off-duty contractors from the non-public areas of its property even when they seek to engage in Section 7-protected activity unless the contractors (1) work regularly and exclusively on the property, and (2) the employer fails to show that the contractor has one or more reasonably non-tresspassory alternative means of communication. In other words, the employer can prohibit off-duty contractors from its property where they seek to use it for union organizing activities if the contractors do not work regularly or exclusively on the property and/or they have alternative means of communication that do not require using the property. Under the UPMC case, which is current Board precedent, employers have the right to refuse union access to even public spaces on an employer’s property.
Under the new Board, the state of the law is likely to return to the New York New York Hotel and Casino standard, under which employers could not restrict off-duty employees from using non-work areas to distribute pro-union literature. Similarly, the UPMC standard is likely to be overturned in favor of the prior Sandusky Mall standard, under which employers could not restrict a union from using public spaces on an employer’s property for union organizing activity if the employer permitted other commercial, civil, and charitable activities in that space. Close scrutiny by employers of the current Board precedent, and changes in this area, is advised where the company is facing union organizing activities, in order to avoid the filing of an unfair labor practice charge and possible implementation of a bargaining order.
d. Expansion of Interpretation of Protect Concerted Activity
Employers can also expect an expanded interpretation of Section 7 “protected concerted activities” under the new Board and general counsel. This may include expanded rights of employees to use their employer’s communication systems for protected activity. The general counsel memo specifically identifies cases in which an employee’s right to use the company email system (or other company communication systems such as Discord, Slack, or Groupme) for protected workplace communication should be given special attention. The memo identifies the current Board precedent as involving “Board Doctrinal Shifts” (from the prior Purple Communications standard, which held that employers must permit their employees to use company email systems to engage in protected activity to the current Rio All-Suites Hotel and Casino, which overruled Purple Communications and permits employers to restrict such employee email communications). The general counsel memo also identifies current board precedent that narrowed the scope of protected activity as requiring reexamination. Specifically it references current Board precedent that employees who acted on behalf of interns were not engaged in protected activity because it was not for “mutual aid and protection.” This signals that the general counsel and Board will seek to expand the definition of “mutual aid and protection” and thereby the definition of protected concerted activities. With these and other related examples, employers can expect a return to an expanded view of protected concerted activities, which will restrict the actions employers can take with respect to such activities even if the actions are impermissible under current law.
These are just some of the examples of changing precedent from the NLRB that are likely to affect unionized and nonunionized employers alike. As with the quickly changing legal environment respecting vaccine mandates, automotive employers should stay up to date on new decisions from the NLRB (and be aware of enforcement priorities of the general counsel) in order to avoid labor-related liability in 2022 and beyond.
As these examples highlight, automotive employers face unique challenges in 2022 due to a frequently changing legal landscape. Employers should be vigilant regarding updates to the current state of the law in these and other areas.
OEMs Expanding Suppliers Responsibility for Ordinary Warranty Claims
AUTHORS | |||||
Vanessa Miller | vmiller@foley.com | |||||
Jeff Soble | jsoble@foley.com | |||||
Leah Imbrogno | limbrogno@foley.com |
In today’s uncertain times, companies across the supply chain are trying to find ways to regain their edge and hedge against risks. Most contracts between Original Equipment Manufacturers (OEMs) and their supply bases already contain buyer-friendly terms that incorporate by reference the OEM’s standard terms and conditions of purchase. Those terms contain broad warranty provisions that, among other things, require the parts to meet all specifications, be free from defect, conform to all laws, be merchantable, and be fit for the intended purpose. These provisions are intended to protect an OEM in the event that there is a warranty issue, warranty campaign, or recall such that the OEM can turn to the supplier to recover damages if the OEM can show that the supplier failed to meet one of the requirements in the broad warranty provision.
In an effort to increase their bottom line, OEMs are now aggressively passing down costs to suppliers by requiring suppliers to agree to pay a portion of “ordinary warranty charges.” Ordinary warranty can refer to any dealer repair that does not rise to the level of a warranty campaign or recall. To recover for ordinary warranty, the OEM does not need to show that the supplier’s part was defective or that it failed to meet an express warranty. Instead, the OEM’s policy may just provide a formula for assessing ordinary warranty charges against its supply base, regardless of fault.
Although many OEMs have had ordinary warranty policies in place for years, through supplier handbooks or separate ordinary warranty contracts OEMs now are advising their supply base that they will be strictly enforcing these policies. Suppliers should be prepared to analyze these charges, negotiate limitations or clarifications to the policy and how it will be applied, and avoid associated pitfalls since these costs can accumulate quickly. In addition, the anticipated total ordinary costs for the life of the program that the supplier may incur need to be taken into account when providing a quotation for new business.
What is an Ordinary Warranty Agreement?
“Ordinary warranty” is the phrase used to describe standard one-off warranty claims of customers that do not rise to the level of necessitating a warranty campaign or recall. Typically, ordinary warranty agreements are found in the OEM’s supplier manual or a standalone ordinary warranty contract that covers all parts/programs, and they describe a predesignated split of costs associated with ordinary warranty claims. Depending on the agreement and the parties’ relative bargaining strength, there may be a flat percentage split of any ordinary warranty claims implicating the part sold — whether by dealer code or description — or there may be a sample of parts analyzed for failure to obtain a percentage of fault attributable to the supplier, which is then extrapolated across the universe of failed parts and future failures.
With warranty campaigns and recalls, if an OEM seeks to impose charges on a supplier, they must be able to tie the defect to a breach by the supplier; there needs to be some nexus to the supplier’s warranty obligations. This is not the case under standard ordinary warranty agreement language. Ordinary warranty agreements exist outside the realm of “cause” or “fault” and instead impose obligations that are tantamount to strict liability. Payments related to ordinary warranty claims are expected to be made without a detailed root cause investigation or determination.
What Key Changes Should Suppliers Watch For?
In the past, even though many OEMs had policies in place that allowed them to pass down ordinary warranty costs to suppliers, OEMs would largely undertake the financial responsibility for these damages. In the wake of the backlash of COVID-19 and global supply chain disruptions, OEMs seeking ways to increase cash flow are starting to be more consistent and aggressive in pushing down ordinary warranty costs to suppliers. OEMs are demanding that suppliers split or completely cover ordinary warranty costs. OEMs also are requiring suppliers to provide replacement parts free –of charge and sticking suppliers with costs associated with expedited shipping and freight to dealers.
Issues with Ordinary Warranty Charges
There are numerous issues surrounding ordinary warranty charges. The most obvious issue is that there is no requirement that the warranty issue be definitively tied to the supplier’s part defect or breach. Under many ordinary warranty agreements where a “strict liability” standard is implicated, for the supplier to foot the bill it can be enough for a dealer simply to log a code implicating the supplier’s part or for a very small sample of parts to show failures without necessarily establishing the cause of those failures (usually analyzed solely by the OEM). Having to bear these ordinary warranty charges certainly will drive up costs for suppliers and drive down profitability.
Suppliers preparing to navigate ordinary warranty agreements and charges should consider the following:
- First, as mentioned above, there may be no root cause analysis undertaken before ordinary warranty charges are passed on to suppliers. This means that the OEM may seek to hold the supplier responsible for the warranty claim even if there is no clear tie to any breach by the supplier or defect in the supplier’s part, and sometimes even if it is not confirmed that the issue is with the part that the supplier provided to the OEM.
- Second, ordinary warranty agreements do not often include provisions that prohibit the OEM from recovering charges against more than one supplier. Presumably, if an ordinary warranty claim implicates multiple parts or an assembly, then the OEM could attempt to recover costs against each supplier involved, leading to potential double-recovery for the same warranty charge. The supplier should be able to access data ensuring that assembly-level failures are properly allocated or that there is some analysis applied to ascertain the responsible supplier.
- Third, if there is a sampling of failed parts or a cursory analysis undertaken by the OEM as part of its ordinary warranty process, then the supplier should ask to be involved and/or conduct its own analysis of a sample of failed parts. It would be best to negotiate this requirement into the ordinary warranty agreement.
- Fourth, warranty codes used by dealers may have accuracy issues. Often, one code is used to cover multiple warranty issues, making it difficult to differentiate the cause of the problem without a full-blown root cause investigation. Dealers also often rely upon “NTF” or “No Trouble Found” codes, meaning that the customer’s issue could not be replicated or duplicated. Despite this, the supplier still is expected to incur the costs of the ordinary warranty charge unless there is an explicit exception in the ordinary warranty agreement for NTF codes.
- Fifth, ensure that your team understands and is comfortable with the OEM’s ordinary warranty process, including the ability to identify errors in charges, the timing and mechanism for objecting to such charges, what charges may be included, and the process used to identify the supplier’s share of ordinary warranty costs.
- Sixth, these costs need to be taken into account for all future parts/programs going forward. They should be part of a supplier’s cost walk since the OEMs now have indicated that they are shifting these risks and costs to their supply base.
Takeaways
Suppliers must be ready in the event that OEMs try to impose new ordinary warranty agreements or enforce agreements already in place. This can result in unexpected financial liabilities, including costs for repair, replacement parts, labor (at rates set by the dealer network), shipping, and handling. Now is the time to revisit your OEM contracts and supplier manuals to ensure you know the terms of any ordinary warranty agreement already in place, and be prepared for OEMs to enforce those terms or impose new terms.
Suppliers should negotiate with OEMs to ensure that any ordinary warranty charges imposed on the supplier are directly tied to the supplier’s parts. Suppliers also should negotiate a provision prohibiting OEMs from recovering the same ordinary warranty costs from more than one supplier, effectively preventing the OEM from “double-dipping” and recovering from multiple suppliers for the same warranty charge. Suppliers should demand that OEMs provide underlying warranty details and dealer warranty code information. While it may not be possible to conduct root cause investigations for all ordinary warranty charges, having this information will allow suppliers to recognize patterns and push back on charges if something seems amiss. Finally, suppliers should take these costs into account when preparing their quotations for new parts/programs since these policies shift costs that previously were borne by OEMs to the supply base.
Possible Silver Lining: Targeted Acquisitions
AUTHORS | |||||
Ann Marie Uetz | auetz@foley.com | |||||
John Simon | jsimon@foley.com |
Nearly two years after the onset of the coronavirus pandemic, as the automotive supply chain continues to be disrupted not only by the pandemic but also by port and logistics delays, shortages in materials such as semiconductors, steel, resin and foam, and rising costs (including labor especially), there exist opportunities for growth through acquisition. Companies that were perhaps propped up with government support early on during the pandemic (through PPP loans or other government aid) are beginning to feel increased pressure as they face financial and operational challenges. Lenders who previously provided extensions of credit and forbearance of defaults are becoming increasingly active in asserting their rights and remedies in the case of a default. The cash flow and credit issues these companies face may result in opportunities to purchase them at depressed valuations. While these deals may appear to be hard to come by, shrewd investors will be well served by considering both out-of-court and bankruptcy acquisitions of the distressed companies that are under pressure due to the current environment.
Checklist of Certain Key Considerations for an Out-of-Court Acquisition
- Often structured like a normal asset deal.
- Due diligence is even more critical to understand in order to avoid and creatively address potential liabilities.
- Specify assumed liabilities and excluded liabilities.
- Include indemnification and escrow where possible (but seller might not be able to perform under indemnification).
- Negotiations with creditor constituencies can reduce exposure.
PROS | |
– Fast; no court approvals required. |
CONS | |
– Cannot “cherry pick” contracts as easily as in bankruptcy. |
Checklist of Certain Key Considerations for Bankruptcy Sale
- Buyers often seek to avoid possible successor liability and other risks, and require the sale to occur in a Chapter 11 to maximize buyer protections/rights.
- Section 363 of the Bankruptcy Code permits a debtor to sell substantially all of its assets if supported by reasonable business judgment, free and clear of all liens, claims, and encumbrances.
- Section 365 of the Bankruptcy Code permits a debtor to assume and assign, or reject, certain contracts and unexpired leases notwithstanding restrictions on assignment in such contracts.
- Upon a bankruptcy filing, the “automatic stay” arises and protects the seller’s assets from creditor collection efforts and contract terminations to enable a transaction to occur.
PROS | |
– Court-approved sale is “free and clear” of liabilities, and balance sheet is clean. |
CONS | |
– Sale will be to the “highest and best bid;” an auction is generally required and, notwithstanding stalking horse advantages, marketing process may yield an alternative winning bidder. |
The automotive industry has faced incredible headwinds, many of which persist into 2022. As companies look to grow their revenue and profits, these headwinds may well present opportunities for growth through acquisition.
Preparing for Automated Vehicle Regulations and Enforcement in the Face of Stalled Legislation in 2022
AUTHORS | |||||
Christopher Grigorian | cgrigorian@foley.com | |||||
Nicholas Englund | nenglund@foley.com |
Over the past few years, there have been many discussions among federal, state, and automotive industry stakeholders regarding the need to remove regulatory barriers that may constrain development and widespread deployment of automated vehicles (AVs) and automated driving systems (ADSs).1 The U.S. Department of Transportation (U.S. DOT) and National Highway Traffic Safety Administration (NHTSA or Agency) have issued several policy statements regarding AVs and advanced driver assistance systems (ADAS), published multiple rulemaking documents, and held several public meetings seeking comments on removing regulatory barriers. In addition to these efforts, Congress, the automotive industry, consumer advocates, and other interested stakeholders have worked collaboratively to draft proposed legislation to facilitate advances in automated technologies and to clarify the distinct regulatory roles of state and federal governments.
Despite these efforts, persistent challenges continue to slow progress, even as the underlying technologies begin to see wider deployment. What future legislation and regulations at the federal and state level will look like remains unclear. In the meantime, NHTSA will likely continue to exercise its authority over safety-related defects to learn about current technologies through informal and formal information requests and to push back on technologies that NHTSA believes may pose a safety risk.
NHTSA will use its safety-defect authority to address emerging automation technologies.
NHTSA published an Advanced Notice of Proposed Rulemaking (ANPRM) in October 2018, seeking comments on a pilot program for collaborative research on motor vehicles with high or full driving automation. More than three years later, NHTSA appears poised to withdraw this rulemaking as it considers a new rulemaking titled “Expansion of Temporary Exemption Program to Domestic Manufacturers for Research, Demonstrations, and Other Purposes” (Proposed Exemption Program), as described in the U.S. DOT’s Fall 2021 Unified Agenda of Regulatory and Deregulatory Actions) (Fall 2021 Unified Agenda). Under 49 U.S.C. § 30114(A), NHTSA has authority to exempt a motor vehicle or motor vehicle equipment from applicable federal motor vehicle safety standards (FMVSSs) on terms that NHTSA decides are “necessary for research, investigations, demonstrations, training, competitive racing events, show, or display.” Although the language is not limited to importations, the exemption authority originated in joint importation regulations originally promulgated by NHTSA and Customs.2 Based on this history, NHTSA has limited use of this exception to imported vehicles. Recognizing the disparity between domestically produced and imported vehicles with respect to the exemption authority in §30114(A), NHTSA explained, in its publication of the Proposed Exemption Program, that it would evaluate whether it could “level the playing field by expanding the coverage of exemption under that section to any vehicle, regardless of whether it is domestic or foreign, that meets the criteria of that section, particularly vehicles with high and full driving automation that do not meet existing standards and whose manufacturers are or seek to become engaged in research and demonstrations involving those vehicles.” 83 Fed. Reg. 50872, 50882 (Oct. 10, 2018). Formally extending these exemptions to domestically produced vehicles would be welcome relief to entities manufacturing and/or testing them. As discussed below, manufacturers could use this rulemaking as an opportunity to obtain guidance related to permissible uses (other than destruction) for decommissioned test vehicles.
Other notable rulemaking activities listed in the Fall 2021 Unified Agenda, related to automated technologies, include:
- The Federal Motor Carrier Safety Administration (FMCSA) intends to amend the Federal Motor Carrier Safety Regulations (FMCSRs) to ensure safe deployment of ADS technologies in commercial motor vehicles (CMVs). The proposal would make changes to requirements related to operation, inspection, repair, and maintenance to recognize the difference between human operators and ADSs.
- NHTSA is analyzing comments to its 2019 ANPRM related to replacing rearview mirrors with camera systems.
- NHTSA intends to propose safety standards that would require automatic emergency braking in passenger cars and heavy trucks.
- NHTSA intends to issue in 2022 a final rule that would address regulatory barriers in crashworthiness safety standards and facilitate certification of vehicles without traditional driver controls. (NHTSA made public a draft of a final rule related to this rulemaking at the end of the Trump Administration, but the draft was never published in the Federal Register and the Biden Administration paused rulemakings that had not already been published.)
Manufacturers should monitor these rulemakings and advocate for standards that are technologically neutral and do not constrain future developments.
NHTSA will use its safety-defect authority to review the safety of emerging automation technologies.
NHTSA’s rulemaking authority requires safety standards to be practicable, meet the need for motor vehicle safety, be stated in objective terms, and be “appropriate for the particular type of motor vehicle or motor vehicle equipment.” 49 U.S.C. § 30111(a), (b)(3). These constraints make the process for developing safety standards – particularly related to emerging technologies – long and difficult. In contrast, NHTSA’s authority to investigate potential safety-related defects provides the Agency with broad and flexible powers that the Agency can quickly deploy to ensure that emerging technologies satisfy the Agency’s interpretation of its existing safety requirements.
Over the past year, NHTSA has demonstrated its willingness to use its investigatory and information-gathering tools to police ADAS and ADS technologies. In June 2021, NHTSA issued Standing General Order (SGO) 2021-01, requiring more than 100 vehicle manufacturers, suppliers, and vehicle operators to report certain crashes that involve vehicles using Level 2 (L2) ADAS and L3 and above automation to the Agency. NHTSA stated that it issued the SGO to obtain information on potential safety defects and to evaluate manufacturers’ compliance with legal requirements to timely identify and conduct recalls for safety-related defects. “Given the rapid evolution of these technologies and testing of new technologies and features on publicly accessible roads, it is critical for NHTSA to exercise robust oversight over potential safety defects in vehicles operating with ADS and Level 2 ADAS.” NHTSA SGO 2021-01 at p. 2.
NHTSA did not issue the SGO 2021-01 in conjunction with an investigation. The Agency explained that it issued the SGO to be consistent with NHTSA’s mandate to prevent harm and not wait for injuries or deaths to occur. See id. These statements demonstrate NHTSA’s intention to vigorously investigate automated technologies and related concerns such as distractions that may inhibit drivers from retaking control of the vehicle.
Manufacturers should anticipate liberal use of information requests not only to the manufacturer whose vehicles are the subject of a NHTSA investigation, but also to suppliers (including suppliers of software and other components of the ADAS and ADS systems) and peer manufacturers. Moreover, NHTSA’s Chief Counsel has authority to issue special orders that are not directly connected to a specific defect investigation. As more ADAS technologies and AVs are deployed, we expect the Agency to use these investigative and information-gathering authorities to “exercise robust oversight.” Id.
But what can we do with decommissioned test vehicles?
Certain vehicle manufacturers are permitted by statute to deploy test and prototype vehicles that do not comply with, and have not been certified to comply with, otherwise applicable federal motor vehicle safety standards (FMVSSs). See 49 U.S.C. § 30112(b)(10). But vehicles using this exception must be used “solely for purposes of testing or evaluation by a manufacturer that agrees not to sell or offer for sale the motor vehicle at the conclusion of the testing or evaluation.” Id. This provision is intended to facilitate the deployment of test vehicles that may not, or could not, be certified as meeting all applicable FMVSS. But it also prevents these test vehicles from being sold or otherwise becoming available to consumers. The “solely” language indicates that the vehicles, at least in the condition in which they were tested, cannot be sold at the conclusion of the testing or evaluation. Yet, the exception does not address what can be done with decommissioned test vehicles. Can the manufacturer modify the vehicle to remove the ADAS technologies and sell the vehicle as a conventional motor vehicle? Can the manufacturer export the vehicle to another country? Must the vehicle be destroyed? What amount of re-manufacturing would render the test vehicle sufficiently different to deem it a different vehicle? The statute does not address these questions, and NHTSA has not taken a position.
Some state regulations pose similar problems, which affect testing entities more broadly than vehicle manufacturers. For example, the State of California developed extensive regulations related to testing and deploying AVs. As part of that process, California now issues an “autonomous vehicle” title when registering these vehicles. Yet, California does not have a process for retitling a vehicle once it has been decommissioned, such as where an AV operator removes the ADS technology stack from a vehicle. Because California restricts who may operate AVs, a vehicle with an AV title may not be able to be sold, and the operating conditions placed on the vehicle by California’s autonomous vehicle regulations arguably would continue to apply to a decommissioned vehicle.
Manufacturers concerned about the environmental impacts should consider these uncertainties when producing test vehicles. Manufacturers should develop plans for decommissioning vehicles and work with state regulators to determine the restrictions that apply to these former test vehicles. The industry should also consider addressing these questions in a future rulemaking related to testing exemptions.
—————————————————–
1 A brief note regarding the terminology used in this article: To be consistent with the SAE Taxonomy, this article uses the terms “automation” and “automated in reference” to vehicle technologies that perform dynamic driving functions, rather than autonomous vehicles. The distinction between automation and autonomous is as follows: “Automation” describes vehicle technologies that control discrete driving functions through software, while “autonomous” implies that the vehicle itself determines all driving functions, routes, and destination without outside input. In the hope of maintaining this distinction, we will use the term “automated vehicle” rather than “autonomous vehicle.” Some regulations do not maintain this distinction – for example, the California Code of Regulations uses the term “autonomous vehicle.” See 13 Cal. Code Reg. § 228.02(b) (defining “autonomous vehicle” as having “the capability of performing the dynamic driving task without the active physical control or monitoring of a natural person”). In contrast, the U.S. DOT “The Automated Vehicles Comprehensive Plan” and NHTSA rulemaking documents refer to automated vehicles and automated driving systems (ADS). See here: https://www.transportation.gov/sites/dot.gov/files/2021-01/USDOT_AVCP.pdf.
>2 On October 31, 1988, Congress amended the National Traffic and Motor Vehicle Safety Act of 1966 by passing the Imported Vehicle Safety Compliance Act of 1988 (the 1988 Act). As the name suggests, the 1988 Act revised the statutes and regulations related to importing vehicles and equipment. The 1988 Act first codified the special exemption authority in what is currently § 30114(A). These exemptions originated in joint regulations promulgated by NHTSA and Customs in the early 1970s. See 19 CFR § 12.80(b)(1)(vii) (permitting temporary importation of a vehicle solely for the purpose of show, test, experiment, competition, repair or alteration).
EV Outlook: Market, M&A, Supply Chain, and Regulatory Trends
Overview
AUTHORS | |||||
Mark Aielllo | maiello@foley.com | |||||
Amanda Beggs | abeggs@foley.com | |||||
Chris Boll | cboll@foley.com | |||||
Nick Englund | nenglund@foley.com | |||||
Steve Hilfinger | shilfinger@foley.com | |||||
Ken Johnson | kjohnson@foley.com | |||||
Lynn Parins | lparins@foley.com |
Until recently the adoption of electric vehicles (EVs) in the United States has been slow to gain the same traction as that in other markets around the globe, particularly in Europe and China. That picture has changed dramatically in 2020 and 2021, however, and 2022 promises to drive an even greater acceleration of EV adoption in the United States.
Range anxiety — the fear of running out of battery power, with no available method of recharging in the vicinity — has been one of the leading factors causing consumers to remain hesitant about adopting this new powertrain technology en masse. The lack of charging infrastructure to support EVs in many U.S. markets, especially compared to well-established distribution channels for internal combustion engines (ICEs), has also fueled this anxiety. Although these consumer concerns persist, rapid changes in recent months appear to signal an environment for the accelerated adoption of EV technology in the U.S. These include rapid advancements in battery technologies, recent funding, and regulatory policy announcements by federal and state governments, as well as aggressive investor and industry-led efforts to reduce greenhouse gas emissions.
One of the most transformational events of the past year on this front was the signing into law of the $1.2 trillion Infrastructure Investment and Jobs Act (IIJA) in November 2021. Many in the federal government and automotive industry hope this new law, and its supporting legislative and regulatory agenda, will accelerate the United States’ adoption of EVs by building the infrastructure necessary to support these powertrains and by encouraging consumer adoption. Although the IIJA did not include an increase in, or a modification of, consumer tax credits for the purchase of EVs, as many proponents hoped would happen (and similar provisions appear in the Build Back Better Act, which is currently stalled), it did include nearly $7.5 billion for the investment in and building out of alternative fuel-charging systems. These funding sources would primarily support EV chargers and infrastructure across the country. This monumental commitment to spending — anticipated to be administered largely through the states — is projected to accelerate investment into EV infrastructure around the nation. Nevertheless, there remain questions of whether the IIJA goes far enough to spur meaningful growth and actually achieves the Biden Administration’s goal of deploying EV chargers along the nation’s highway corridors to facilitate long-distance travel. While the federal government’s commitment has been demonstrated through passage of the IIJA, what still lies ahead is the complex task of effective implementation.
The traditional consumer is used to filling up his or her fuel tank and getting anywhere from 300 to 400-plus miles per tankful (with each filling requiring no more than 10 minutes to complete), so perceived challenges in the EV charging process have been a large roadblock to widespread adoption of EVs in the United States. In an effort to overcome range anxiety, Original Equipment Manufacturers (OEMs) have been launching platforms with larger batteries, faster charging capabilities, and more abundant charging networks, but even this will require additional support as the charging network expands, including more robust utility networks, maintenance and support networks, renewable energy resources, standardized charging platforms, and the simple need for more chargers as more EVs enter the market.
As the country looks to its newest chapter in mobility, it is not only consumers who stand to benefit from the rollout of EV charging networks and improved infrastructure. The commercial players in both last-mile/last-kilometer delivery, as well as the logistics and fleet operators, are looking to electrify their platforms. Meanwhile, manufacturers and suppliers will see downstream benefits as their investments in new powertrain systems are realized through further market adoption and investment interest next-generation technologies grow in both private and public market sources.
The prospect of a growing EV market share in the U.S. has not been lost on dealmakers. While the 2020 transaction landscape was briefly interrupted by the COVID-19 pandemic, deal activity in the automotive and mobility sectors continues to accelerate and is approaching all-time highs. While increasing interest rates and inflation may temper activity in the short term, increased interest in EV technology platforms is expected to continue to drive the automotive M&A market and investment activities in OEMs, suppliers, and technology companies that support this burgeoning industry sector.
M&A Market Outlook 2022: Automotive Investments Roll Ahead Despite Roadblocks
A complicated market landscape has now been the auto industry’s norm for nearly two years. Since the beginning of 2020, manufacturers have been hampered by plant shutdowns, social distancing regulations, skyrocketing commodities prices, supply chain delays, and shortages of everything from microprocessors to employees. Adding to the situation are unpredictable changes in consumer demand, inflation worries, and difficult-to-comprehend valuations such as Tesla’s eye-popping trillion-dollar market capitalization.1 Exacerbating the confusion, the industry finds itself in the midst of a sea change caused by a rapid transition to increasingly connected, autonomous, and electrified vehicles. In short, there is a lot going on for market participants to track.
In spite of this, deal activity generally, and in the automotive and mobility sectors specifically, has accelerated at a blistering pace. At the end of Q3 2021, deal activity by volume in the mobility space had already exceeded the 2009 full-year record by more than $50 billion. As 2021 drew to a close, global M&A volumes pushed toward an unprecedented record of $4.33 trillion, overtaking an all-time annual peak of $4.1 trillion recorded before the financial crisis hit in 2007.2 3
In the automotive space, global mergers and acquisitions hit historical highs in 2021, with a total deal value of $136.6 billion — up 111% from 2020. While the onset of the pandemic significantly impacted deal value and volume in 2020, M&A activity recovered in the second half of the year and accelerated with deal volume in 2021 up 19%, to 971 deals, with an average disclosed deal size of approximately $435 million. Of the $136.6 billion of deal value, vehicle manufacturers comprised the largest segment, with $61.3 billion (or 45%).
This unprecedented deal volume, including in the EV sector, has been driven by the rejuvenation of Special Purpose Acquisition Company (SPAC) and de-SPAC transactions, which have allowed privately-held EV companies to reach the public capital market faster than have traditional IPOs. Although public market receptivity to these investments over the past 18 months demonstrates that investors are looking eagerly toward the future of EV technology, with an eye on environmental stewardship, poor performance of some issuers, and increased regulatory scrutiny from the SEC there remain future headwinds for de-SPAC transactions in this space.4
These public market capital increases have been accompanied by significant industry and public-private-partnership investments. In the fall of 2021, GM and LG Electronics filed applications in Lansing, Michigan to build a reported $2.5 – $3 billion battery plant. Toyota announced plans to open a massive lithium battery plant in Liberty, North Carolina, and Ford Motor Company similarly announced plans to invest over $11 billion in battery plants and electric truck plants across Kentucky and Tennessee.5
Other Trends
With so much activity and disruption, the outlook for 2022 is a bit difficult to pin down. Numerous challenges and opportunities confront the industry, including changes in distribution and franchising, right to repair laws, safety and data protection, charging standards, and even tax incentives, to name a few. Nevertheless, amidst so much change a few trends appear to be emerging:
1. Expect a move toward public markets regulatory equalization.
2021 saw unprecedented utilization of SPACs in the automotive space due to their high-speed fundraising capabilities and ability to react to market trends. This velocity has drawn increased regulatory scrutiny, particularly around disclosures of conflicts of interest and dilution, but do not expect SPACs to become a relic of the past. In early December, SEC Chair Gary Gensler pitched new rules around marketing practices, tougher disclosure requirements, and liability obligations, which suggest that SPAC investors of the future will face regulation in parity with traditional IPOs.6 Should these rules come to pass, expect SPACs to revise their marketing strategies to focus more on evidence-based target selection, suffer longer lock-up periods, experience requirements for sponsors and/or investors, and define contractual terms that better protect dilution of shareholder ownership after the acquisition.
2. Supply chain competence may determine success.
With strong demand, continued COVID-19 issues, and inflation concerns, those market participants who can best manage their inherently unstable supply chains will be more likely to come out ahead. The EV supply chain is markedly different than the traditional ICE supply chain in a number of ways.
First, EVs involve mechanically simpler components, but those components generally incorporate more technology, which creates additional challenges and needs. Intellectual property protection and use — including the freedom to operate — become paramount as more technology is developed and utilized in vehicles. Warranties, like those concerning fitness and design, also are subject to specific tailoring, including due to the complex integration of components and systems that is required for EV production.
Next, the supply base for many technologies and components has remained limited both in the size and scope of the base and in the availability of certain materials and capacities. There also is increasing competition from other industries, such as consumer electronics and appliances, for these resources. These shortages and limitations are expected to continue through the upcoming year. Strategies should be considered to proactively address these issues, such as establishing or reevaluating long-term agreements. Addressing anticipated shortages and rising costs in connection with purchase and sales requirements and obligations is necessary. These issues may no longer be viewed as unforeseeable, and allocating the risk and adverse material changes through contracting should be addressed, along with events that may no longer be viewed as falling under “force majeure” or commercial impracticality provisions. Multiple and geographically diverse sources, reserved capacity, increased inventories, and material on hand as well as contingency planning must also be addressed. Finally, transparency and data sharing are topics of increasing interest.
Despite gloomy predictions by some industry players, distressed M&A did not play a significant role in deal volume in 2020 or 2021. However, empty car lots (or those filled with chip-shorted vehicles) across the country — driven by supply chain issues and coupled with huge, pent-up demand — suggest that those able to move product and do so consistently are far more likely to be in a healthier position when markets inevitably slow, giving rise to more troubled supplier situations. If the automotive sector starts to see an increase in distressed M&A, expect the stable, well-supplied, and well-capitalized market participants to look for the opportunistic investments needed to survive and thrive in the coming years. While 2022 and the ensuring years may see an uptick in distressed M&A as volatile input costs and interest rates rise, current estimates are not showing a return to the distressed marketplace of 2008-2009 due to relatively stronger balance sheets and smarter approaches to risk allocation, and matching production to demand.
3. Note environmental considerations for zero-emission vehicles.
Both the U.S. Environmental Protection Agency (EPA) and the California Air Resources Board (CARB) have accelerated their focus on hybrid and zero-emission vehicles (including electric and hydrogen fuel cell vehicles) to achieve emission reductions from cars, trucks, and (in California) off-road equipment.
On December 20, 2021, the EPA finalized its new greenhouse gas (GHG) emissions standards for new passenger cars and light trucks. These new rules are the most ambitious in history, requiring automakers to meet the strictest fuel efficiency standards ever proposed and to do so by model year 2026. While the rule does not specifically require manufacturers to produce zero-emission vehicles, practically speaking these aggressive new standards will likely require automakers to shift production to hybrid and/or zero-emission vehicles within the next four years to achieve compliance with the standards. Such a shift will further increase demand for batteries and other EV powertrain components. To be successful, it will also likely require investments in electric chargers and the transmission upgrades that will be required to maintain grid stability, and/or investments in hydrogen vehicles and fueling stations, as discussed above.7
Similarly in 2020, California also issued the Advanced Clean Trucks Rule requiring that, beginning in 2024, a certain percentage of each truck manufacturer’s sales into California must be from zero-emission vehicles, with a target that by 2045 all new trucks sold in California must be zero-emission.8 In 2020 Governor Newsom also issued Executive Order N-79-20, which established a goal that, where feasible, all new passenger cars and trucks, as well as all drayage/cargo trucks and off-road vehicles and equipment sold in California, will be zero-emission by 2035. The order set a similar goal requiring that all medium- and heavy-duty vehicles will be zero-emission by 2045 where feasible.9 Also in 2021, CARB issued its proposed Advanced Clean Fleets Rule for medium- and heavy-duty zero-emission fleets, with the goal of achieving a zero-emission truck-and-bus California fleet by 2045 where feasible. These goals will be implemented by CARB through various regulations that the agency has issued in some instances and currently is developing in others, and will again increase the demand for zero-emission vehicle components and require investments in electric chargers and transmission upgrades.10 The following states have also adopted rules modeled after California’s Advanced Clean Trucks Rule: Oregon, Washington, New York, New Jersey, and Massachusetts — and other states are also expected to adopt similar rules in the near term.
It is also worth noting for new entrants to the zero-emission vehicle market that both EPA and CARB have certification requirements for zero-emission vehicles that must be met prior to production of the vehicles for sale in the U.S. and/or California. The specific requirements for certification depend on the type of vehicle (light-, medium-, heavy-duty etc.), and California has developed specific certification procedures for zero-emission powertrains. In addition, both agencies have specific labeling requirements and importation requirements for zero-emission vehicles, depending on the type of vehicle and use of the vehicle.
4. Understand NHTSA regulations for commercial EV applications.
The National Highway Traffic Safety Administration (NHTSA), which regulates motor vehicle safety, is planning to amend the federal motor vehicle safety standard (FMVSS) that applies to high-voltage batteries to include heavy- and medium-duty vehicles. FMVSS 305, Electric-powered vehicles: electrolyte spillage and electrical shock protection, currently applies to passenger cars and to multipurpose passenger vehicles, trucks, and buses with a gross vehicle weight rating (GVWR) of 4,536 kg or less (excluding low-speed vehicles). 49 CFR 571.305 S3. The U.S. Department of Transportation’s Fall 2021 Unified Regulatory Agenda includes a proposal by NHTSA to amend FMVSS 305 to include medium- and heavy-duty vehicles.
As the commercial vehicle market expands use of EVs and other vehicles’ high-voltage propulsion equipment, industry participants should monitor the Federal Register for this potential rulemaking. Because heavy- and medium-duty EVs are not currently subject to the performance requirements in FMVSS 305, EV development work should track any proposed requirements. Note that any potential amendments would likely take effect more than a year after publication of the notice of proposed rulemaking.
Another important issue that EV manufacturers are beginning to face is that of the certification requirements for vehicles manufactured in more than one stage and for vehicle alterers. NHTSA has specific requirements related to the manufacturing stage, where the vehicle identification number (VIN) must be assigned and for which manufacturers must certify conformance to relevant FMVSS for each stage of manufacturing. Some of the certification responsibilities depend on the entity that installs the powertrain or swaps out an ICE powertrain for an electric powertrain.
Manufacturers developing vehicles that will involve purchasing the chassis, removing existing powertrains, altering complete/fully certified vehicles, and similar projects should understand these regulatory obligations and how they may impact the vehicles’ path to market; these regulations can influence vehicle development strategies. Understanding these requirements early in the development process will help manufacturers avoid potential complications and added costs that could delay projects or make it difficult to sell vehicles in a particular state.
5. Deployment of EV-charging infrastructure is poised to expand significantly.
In spite of the recent uncertainty over whether the Build Back Better Act will become law in any form resembling that passed by the House in Fall 2021, EV-charging infrastructure may still be on the cusp of a dramatic inflection point.
Beginning with the Biden Administration’s August 2021 Executive Order on Strengthening American Leadership in Clean Cars and Trucks, continuing with the IIJA passed in November 2021, and culminating with the EPA’s new emissions rules published at the end of December 2021, the federal government has implemented an assortment of carrots and sticks meant to stimulate adoption of EVs and the charging infrastructure necessary for widespread public adoption. In addition, public and private industry groups have begun to collaborate to expand the needed infrastructure.
The Executive Order kicked off the EPA rulemaking process concerning new emissions standards for cars and light-duty trucks. The Infrastructure Investment and Jobs Act, as noted above, includes $7.5 billion allocated to invest in a national network of EV-charging infrastructure. How that will be deployed at the state and local levels is not yet finalized. Also as noted above, the EPA GHG rules’ cumulative effects are expected to lead to significant increases in EV car adoption, in turn requiring an increase in the EV infrastructure to support them.
In addition to federal government action, a national network of energy utilities organized through the Edison Electric Institute’s National Electric Highway Coalition (NEHC) has declared its intention to begin immediately to expand EV-charging infrastructure. According to the NEHC fact sheet, the NEHC has 53 member utilities with service territories spanning the country and covering most major U.S. travel corridors.
The NEHC utilities have agreed to work to establish foundational EV fast-charging networks across their service territories. NEHC also cites the major uptick in EV sales that are anticipated through 2030, estimating that nearly 22 million EVs will be in use by 2030, which will require upwards of 100,000 DC fast-charging stations (representing more than 10 times the number of currently available fast-charging stations).
All of these developments together signal immense investments in EV infrastructure to come, and capital is already organizing in order to take advantage of these opportunities. EV infrastructure will come in the form of vehicle-charging equipment installed in “stations” at homes, businesses, and standalone service stations (including potentially integrating with conventional gas stations). Additional expansion and rehabilitation of the electric grid infrastructure necessary to sustain the increased electricity demand from all of these EVs will also be a critical precondition to facilitating the necessary growth in EV infrastructure. This grid infrastructure includes generation, transmission, and smart-grid technologies as grid operators require greater control over the increased load on the system.
Conclusion: There is No Turning Back
Regardless of whether automotive manufacturers and suppliers find themselves in a healthy or challenged position for 2022, an industry consensus has emerged that we are on an irrevocable path to electrification. Climate-neutral mobility and corporate social responsibility are increasingly important priorities for investors and consumers and, as a result, the companies in which they invest and from which they buy vehicles. Batteries and other high-tech electronic components are now more critical infrastructure than engine assembly for many mobility companies, and their increasing adoption has the potential to drive extreme disruption as manufacturers remake their supplier chains to address these new opportunities. With 145 million units of new EV sales expected in the next eight years, all industry players must properly adapt, innovate, and rapidly address even more changes on the horizon.
————————————————–
3 https://www.pwc.com/us/en/industries/industrial-products/library/automotive-deals-insights.html
9 https://www.foley.com/en/insights/publications/2020/10/california-zero-emission-vehicles
10 https://ww2.arb.ca.gov/our-work/programs/advanced-clean-fleets/advanced-clean-fleets-meetings-events?utm_medium=email&utm_source=govdelivery
Driving Sustainability: Automakers Look Beyond Electric Vehicles
AUTHORS | |||||
Dorothy Watson | dwatson@foley.com | |||||
Hillary Vedvig | hvedvig@foley.com | |||||
Bill Re | wre@foley.com |
Electric vehicles typically steal the show in conversations about sustainability in the automotive industry — and for good reason. Emissions from the transportation sector are estimated to account for 29% of all greenhouse gas emissions in the United States.1 From Tesla’s domination in the news to Ford’s record-breaking F150 Lightning, the electrification of vehicles is an exciting step in the energy transition. However, there are more sustainability concerns and opportunities when it comes to vehicles than how a car is powered. The goal of sustainability is to meet our own needs without compromising the ability of future generations to meet theirs, which includes recycling, reusing materials, and moving to processes that emit less carbon. Therefore, the sustainability of the vehicle itself — from what it is made of to how it can be recycled — should not be left out of the conversation.
I. Sustainable Chassis
The bodies of traditionally mass-produced consumer vehicles are made from steel and aluminum. Now, manufacturers are moving toward more sustainable materials as well as vehicles that are lighter overall, thereby improving fuel efficiency. A new initiative, called the Circular Cars Initiative by the World Economic Forum, is looking for opportunities to establish closed-loop recycling of aluminum and steel from vehicles.2 In particular, while new aluminum is very costly and resource-intensive to mine, it is virtually infinitely recyclable. Global demand for aluminum is projected to grow by more than 80% by 2050, and recycled aluminum uses just 5% of the energy required for primary production to produce.3 Accordingly, by increasing the use and reuse of aluminum in vehicles, automakers are shifting to a more renewable and fuel-efficient resource.
While the Circular Cars Initiative is voluntary, European Union Directive 2000/53/EC, End Life of Vehicles (the “Directive”), requires member states to implement measures aimed at the prevention of waste from vehicles.4 The Directive also aims at the reuse, recycling, and other forms of recovery of end-of life vehicles and their components. The goal of the Directive is to reduce the disposal of waste as well as improve the environmental performance of all of the economic operators involved in the life cycle of vehicles, especially the operators directly involved in the treatment of end-of life vehicles.
In addition, a lighter alternative to steel and aluminum is plastic. Automakers are looking toward ocean plastic — swirling “islands” of plastic waste in the ocean5 — as raw material for automotive parts and structures; automaker Ford has announced that the Bronco Sport’s wiring harness clips will be made from discarded plastic fishing nets taken from the Indian Ocean and Arabian Sea.6 In line with the circular economy ideas outlined above, Ford also uses recycled water bottles to produce lightweight, aerodynamic-enhancing, and noise-reducing underbody shields on the 2020 Ford Escape.7 Further demonstrating its leadership in sustainability, Ford has announced plans to work with McDonald’s to use dried coffee bean skins and turn them into reinforced headlamp housings, and it is also looking at using U.S. currency taken out of circulation, and agave fiber from the tequila-making process, to make other parts for its cars.8
While Ford is a standout leader in sustainability initiatives, other automakers are making notable headway in sustainable practices as well, such as GM committing to using at least 50% sustainable material content in its vehicles, measured by total vehicle weight, by 2030.9 And Toyota has established a Global 100 Dismantlers Project in order to establish systems for appropriate treatment of end-of-life vehicles through battery collection and car recycling. Toyota aims to have 15 vehicle recycling facilities by 2025.10
II. Sustainable Interiors
Inside the car, upholstery presents another opportunity for increased sustainability. The movement toward natural fibers in vehicle interiors is a growing trend.11 Even back in 2005, more than 30,000 tons of natural fibers were used in the automotive industry in Europe, and in 2015 the figure reached 50,000 tons, of which 10% to 20% were European hemp fibers.12
Recently, Ford has begun incorporating post-consumer discarded carpet and recycled tires for interior car components.13 Econyl nylon — a new material made from recycled industrial plastic, fabric offcuts from clothing manufacturers, and abandoned fishing nets recovered from the ocean — can be used for floor mats and other trim.14 Mercedes-Benz has been using Dinamica, a sueded fabric made from recycled plastic and fibers, to cover seats and Karuun, a compressed timber product, as floors and dashboard trim.15 Lenzing, an Austria-based fiber producer, also is working to bring sustainable fibers to the automotive industry.16 Using sustainably produced wood-based materials, they are able to make textiles that can become compost material after they are removed from a vehicle, rather than ending up in a landfill or in rivers and oceans.17
III. Sustainable Tires
Nearly 250 million scrap tires are generated annually in the U.S. alone, making this one of the historically least sustainable parts of a vehicle.18 The U.S. Tire Manufacturers Association is working toward eliminating historical scrap tire stockpiles while growing economically- and environmentally-friendly scrap tire markets.19 Such scrap tire markets include use as landfill covers, railroad lines, rubberized floors and asphalt, and playgrounds. The number of stockpiled scrap tires decreased from over one billion in 1990 to about 67 million in 2015 — a 93% reduction.20 However, there is still a long way to go in making the tire component of vehicles sustainable. Some tire manufacturers are developing tire products using oils from sunflowers and natural latex rubbers, such as organic waste that comes from plants, to be used to make bio butadiene, a type of synthetic rubber used in tires.21
In addition, tire manufacturers are looking at recycling polystyrene foam packaging into tires by creating a sustainable synthetic rubber.22 Importantly, polystyrene is a waste stream that is otherwise not reused, so creating a reuse market for polystyrene is particularly sustainable. Similarly, PET plastic waste from items such as water bottles can be recovered, broken down, and reformed into polymer reinforcements in tires. Tire manufacturer Michelin announced plans for recovering 90% of materials from waste tires for reuse in a variety of rubber-based products, including not only new tires but also conveyor belts and anti-vibration products for automobiles.23 With this technology, 56 million tires could be recycled each year to make new Michelin tires and other useful products.24
Tire material innovations and recycling technology can be used in support of a circular, sustainable economy for the tire industry that will enable virtually everything in an end-of-life tire to be recovered for reuse, transforming one of the least sustainable parts of a vehicle into one of the most.
IV. Legal Considerations in Sustainability
While the auto industry is evolving to address sustainability, new legal risks and opportunities accompany this change. From regulatory changes to reporting obligations to litigation risk, companies need to be mindful of legal issues surrounding sustainability issues.
First, it is important to remember that not all movements toward sustainability are entirely voluntary. Governments recognize that encouraging circular economies, where materials in products are reclaimed and reused over and over, will be the key to tackling resource shortages and hazardous materials impacts. Look for regulatory bodies to increasingly step into this space through programs like reclamation and reuse standards, and take-back mandates. Because of this, even auto industry members not actively pursuing sustainability goals should keep an eye on emerging sustainability programs around the globe.
For companies that are moving quickly to incorporate sustainable choices into the automotive industry, Environmental, Social, and Governance (ESG) reporting frameworks include opportunities to tout this progress. While ESG reporting is not currently mandated by law in the U.S., many investors and stakeholders are looking to ESG reports to identify companies that are forward looking and sustainable. In many investor’s eyes, the kinds of sustainable choices mentioned in this article can demonstrate a business’s adoption of forward thinking that has an impact on financial sustainability. Further, through ESG reporting, some companies will be able to demonstrate that they are mitigating significant risks like resource shortages through some of their sustainability initiatives.
However, companies should beware of overpromising and under-delivering on sustainability. Sustainability claims — including claims used in marketing and promotions as well as in ESG reporting — must be thoroughly vetted to reduce potential exposure to greenwashing litigation. Companies should avoid broad claims like “sustainable,” “clean,” and “conscious,” and instead clarify and quantify the kinds of sustainability benefits their products achieve. Importantly, companies must develop and maintain robust documentation that supports any sustainability claims they do make.
Lastly, in many instances supply chain management will be critical to achieving sustainability goals while minimizing accompanying risk. However, sustainable sourcing contracts and processes will need to address different risks than traditional supply chain agreements. For example, contracts addressing the supply of reclaimed materials need to address sustainability — specific terms and conditions like restricted or prohibited sources and post-consumer content composition. Third-party suppliers of take-back and reclamation services will need to be vetted and audited to avoid claims of improper waste management. Contracts should obligate suppliers of sustainability-related products and services to cooperate with efforts to substantiate sustainability claims or defend against allegations of greenwashing.
Automakers today are driving toward sustainability with innovative approaches to material selection, recycling, and reuse. These exciting changes present significant opportunities for companies that stay ahead of challenges like greenwashing claims, ESG litigation, and supply chain issues.
——————————————————
1 https://www.epa.gov/greenvehicles/fast-facts-transportation-greenhouse-gas-emissions
2 https://www.weforum.org/projects/the-circular-cars-initiative
4 https://eur-lex.europa.eu/legal-content/EN/TXT/?uri=celex%3A32000L0053
5 https://www.biologicaldiversity.org/campaigns/ocean_plastics/
6 https://hypebeast.com/2021/12/ford-bronco-sport-recycled-ocean-plastic-sustainability
7 https://hypebeast.com/2021/12/ford-bronco-sport-recycled-ocean-plastic-sustainability
9 https://www.gmsustainability.com/_pdf/resources-and-downloads/GM_2020_SR.pdf 0
10 https://etfdb.com/esg-channel/esg-case-study-toyota/
11 As opposed to synthetic fibers that consume more material and energy to produce. However, not all “natural” fibers are an appropriate replacement. For example, while cotton is “natural,” large amounts of water, pesticides, chemicals and energy are needed to prepare and dye the fabric during cotton degradation and processing. https://jcsr.springeropen.com/articles/10.1186/s40991-020-00057-z
12 https://jcsr.springeropen.com/articles/10.1186/s40991-020-00057-z
15 https://www.nytimes.com/2020/06/04/business/sustainable-materials-cars.html
16 https://www.automotiveworld.com/articles/auto-industry-turns-attention-to-sustainable-interiors/
17 https://www.automotiveworld.com/articles/auto-industry-turns-attention-to-sustainable-interiors/
18 https://www.ustires.org/sustainability-driving-force-us-tire-manufacturing-industry
19 https://www.ustires.org/sustainability-driving-force-us-tire-manufacturing-industry
20 https://www.ustires.org/sustainability-driving-force-us-tire-manufacturing-industry
21 https://www.aftermarketnews.com/the-future-of-tires-sustainable-airless-connected/
22 https://www.aftermarketnews.com/the-future-of-tires-sustainable-airless-connected/
24 https://www.michelin.com/en/innovation/vision-concept/sustainable/
Putting Brakes on Cybersecurity Threats: Practical Strategies to Mitigate Cybersecurity Risk
AUTHORS | |||||
Jen Urban | jurban@foley.com | |||||
Aaron Tantleff | atantleff@foley.com | |||||
Avi Ginsberg | aginsberg@foley.com |
What would you do if you woke up tomorrow and your company’s IT systems were completely locked down? What if you could not use phones, check emails, or receive orders? What if you could not operate machinery or pay payroll? What if the sensitive, personal, and proprietary information your company stores was suddenly unavailable and potentially for sale on the black market? What loss would your company sustain each hour it was offline? What would you do if your company was the subject of a regulatory investigation? What would you do if the media exposed that your company was shut down due to a cyber attack? What would you tell the board or your shareholders? Unfortunately, this is the reality many companies suddenly face today when they become the victim of a ransomware attack.
In addition to being the victim of an attack by a threat actor, these companies may become the target of lawsuits alleging a variety of harms, including failure to deliver on contractual promises, exposure of sensitive information, and/or violation of various laws due to the company’s allegedly negligent cybersecurity practices. Many of these lawsuits result in large settlements for plaintiffs, as reasonable cybersecurity practices are now the standard of care expected of all businesses and many are not adequately prepared. The practical strategies in this article can help ensure your business is on the path to preparing for and safeguarding against a ransomware attack and other cybersecurity risks.
Ransomware: A Substantial Threat to the Automotive Supply Chain
Ransomware attacks frequently made headlines in 2021 and had a substantial impact on many U.S. companies. In the first six months of last year alone, ransomware attacks on U.S. companies were up 148% from 20201. These attacks were responsible for impacting the availability of gasoline up and down the East Coast, disrupting multiple meatpacking plants, and as the year came to a close, causing a cream cheese shortage (which frustrated many holiday bakers). While there are numerous cybersecurity threats affecting companies, such as phishing attacks and software vulnerabilities, these threats are now being utilized as a vector to infiltrate company systems and launch ransomware attacks.
The automotive supply chain is a prime target for ransomware attacks. The cyber criminals that perpetrate these attacks (threat actors) are smart, organized, and creative. They frequently research their victims and target the companies they believe will be most likely and able to pay a ransom. Increasingly, they are targeting industries and companies that they believe will be substantially affected by downtime. The historically just-in-time nature of many parts of the automotive supply chain makes it a prime target for these attacks, as threat actors know such companies cannot afford to be offline for several days or weeks and are more likely to pay a ransom to get back up and running as quickly as possible.
The U.S. Federal Government and many other governments are increasing efforts to combat ransomware, including issuing statements and guidance for the public and private sectors. Unfortunately, due to rapidly evolving technologies, changing global payment systems, and countries that harbor cyber criminals, this pervasive threat is extremely difficult to eradicate. This means it is vitally important for all companies in the automotive supply chain to understand how a ransomware attack could impact their operations, take steps to minimize the chances of an attack occurring, and make changes to minimize the potential damage should an attack occur.
Costs of a Ransomware Attack
Ransomware attacks can be devastating. Many companies in the automotive supply chain cannot operate without computers — they control key machinery, keep track of production and orders, and operate safety systems, such as clean air systems, necessary for production. Yet in a matter of minutes ransomware can lock down computer systems, making them inoperable and rendering important information inaccessible. Further, confidential information may be stolen and, in some cases, published online or sold on digital black markets. Companies are then faced with a tough decision: pay a ransom to unlock their computer systems and prevent confidential information from being leaked or try to erase and restore systems from backups.
The obvious impacts of a ransomware attack are the costs and risks associated with production downtime and the cost of a ransom payment. Companies may be wholly or partially unable to operate while systems are locked down by ransomware. Ransom amounts typically range from several hundreds of thousands to millions of dollars, and even after payment it can take days to fully restore computer systems. In addition to these costs and risks, there are many less-obvious costs:
- Restoring Computer Systems. Restoring computer systems can be costly. Even if the ransom is paid, trained professionals may need to be hired in order to properly use the specialized software provided by the attackers to restore systems to their pre-attack working state. In addition, companies that suffer a ransomware attack typically hire a computer forensics vendor to determine exactly how their systems were infiltrated and what actions the attackers took while inside, so they can be remediated to prevent additional attacks in the future. (If you leave the back door open, you will likely be attacked again!)
- Legal Compliance. Depending on the systems and information impacted by ransomware, a company may be required to comply with various state data breach notification requirements, department of defense notification requirements, and other applicable laws. In addition, before paying or making a promise to pay a ransom, companies must conduct diligence to ensure payment is not prohibited by U.S. sanctions. The cost of legal compliance is highly fact-specific and can range from a few thousand dollars to hundreds of thousands, depending on the implicated laws and requirements.
- Subsequent Litigation. If certain personal information, such as certain information contained in a typical employee human resources file, is exfiltrated during a ransomware attack, there may be lawsuits filed against the company. Resolving such suits can be costly.
- Contractual Violations. Production delays due to a ransomware attack frequently result in violation of contractual requirements as companies are unable to meet obligations to their customers. Depending on the terms agreed upon, a company may be liable to its customers for the customer’s lost profits due to the delays, a multiple of the cost of the product, or the cost for customers to temporarily find a new supplier if one is available. There may be additional liability if the unavailability of inputs or component parts causes a ripple effect resulting in delays downstream.
- Reputation Impact. Delays in production can make a supplier appear unreliable, potentially resulting in customer distrust and loss of future business. In addition, after infecting a company with ransomware, threat actors may contact the company’s customers or business partners to inform them of the ransomware attack in an effort to increase pressure and extort a larger ransom payment, resulting in additional reputational damage.
Practical Cybersecurity Strategies to Mitigate Ransomware and Other Cyber Risks
Ransomware is one of several common cybersecurity risks companies face today. Risks such as theft of intellectual property, insider threats, and business email compromises — in which a threat actor gains access to company email account(s) and uses that access to perform malicious actions such as misdirecting funds, changing order terms or recipients, or stealing sensitive information — are increasingly common. By employing these practical cybersecurity strategies, companies can mitigate risks associated with ransomware as well as many other types of cybersecurity risks.
- Keep computers and hardware patched and up to date. Attackers frequently use vulnerabilities in software to infiltrate company computer systems and launch ransomware attacks. Many of these attacks are avoidable by regularly installing updates and patches that fix security flaws. It is important to keep all network and internet-connected devices up to date, including computers, smart phones, tablets, routers, firewalls, and “smart” technology, including sensors, lightbulbs, and hubs. In addition, industry standard antivirus software should be used on all computers and kept up to date.
- Plan ahead. Your company should have an up-to-date incident response plan covering all types of cybersecurity incidents. Due to the large uptick in ransomware, many companies also find it helpful to have a ransomware-specific policy in place. These documents help to ensure an orderly and efficient response to a cybersecurity incident, which can substantially reduce legal risk and other costs. Legal counsel can assist with drafting or revising these plans and policies to ensure they meet current industry standards and regulatory guidance.
- Do not allow personal devices to connect to company networks. If your company provides internet access to employees or customers, create an isolated guest WiFi network for them to use. Do not allow them to connect to the same network used by company computer systems.
- Regularly train employees on cybersecurity risks. Ensure training covers topics such as ransomware, phishing, spear phishing, social engineering, and forged emails. Employees are frequently the “weakest link” in company security, and untrained employees are more likely to fall for targeted attacks.
- Practice responding to an incident. One of the best ways to improve your company’s response readiness is to regularly practice responding to an incident. Tabletop, or mock, incident response exercises help a company to identify weaknesses in its response plans and prepare incident response team members ahead of a ransomware attack or other cybersecurity incident. This way, if the company is affected by a ransomware attack, critical mistakes can be avoided and incident response team members will be prepared for their duties despite the chaos. Experienced cybersecurity counsel can assist with designing and conducting tabletop incident response exercises.
- Require all employees to use multifactor authentication. Employees should be required to use multifactor authentication on all accounts provided by the company, including computer, email, and VPN accounts.
- Limit employee access. Each employee computer account should be configured with the minimum amount of access required. Do not give employees “administrator” access unless they are trained IT professionals who require such access. Do not allow general employee accounts to install unapproved software or make changes to system settings. Do not allow employee accounts general access to file shares or servers unless such access is needed. Restrict file share access to specific folders where possible. Less access means more difficulty for an attacker if they obtain and try to use an employee’s login credentials.
- Allow remote login only for employees that need it. Ensure only specific employees with a need for remote access can log into VPN or remote desktop services.
- Regularly backup systems and store backups separately. Backups should be kept on a different system (on a different network or offline), or stored with a secure cloud backup provider, to prevent ransomware or other malicious code from impacting the availability of backups.
- Segment your network. Consider moving critical systems to a separate network from the general network used for email, order processing, etc. This helps to prevent ransomware and other malicious code from spreading to critical systems and may help avoid a total business shutdown in the event of a ransomware attack.
- Use email filtering software. Software that filters out malicious links and phishing attacks is an excellent first line of defense and can make it more difficult for attackers to reach employees and infiltrate systems.
- Ensure IT has an adequate and properly utilized budget. Upgrading software and hardware can be costly, but generally it is substantially cheaper than a ransomware attack. Ensure your company’s IT team has an adequate budget for cybersecurity and that they proactively utilize it to improve your company’s cybersecurity defenses. Ask them if your organization follows the IT guidance in this section and how they have prepared for a ransomware attack or other cybersecurity incident.
——————————————————–
1 2021 SonicWall Cyber Threat Report, Mid-Year Update