Accelerating Trends: Assessing the Supply Chain in a Post-Pandemic World
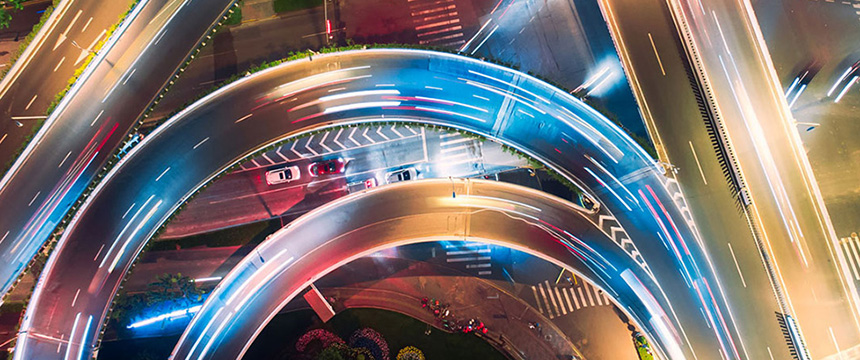
Table of Contents
This report identifies resiliency and innovation considerations for manufacturers and provides frameworks and tools for you to evaluate how those considerations impact your business.
Section 1: Rethinking China
How manufacturers will analyze right-shoring to consider the benefits and costs of a shift in supply chains away from China and toward other countries.
Section 2: Resiliency Review
How manufacturers will review processes to ensure a stable and resilient supply chain, focusing on traceability and continuity of supply through diversification or other viable strategies.
Section 3: Innovation & Efficiency
The accelerated use of new technologies and business processes to facilitate innovation and efficiencies.
Click here to download the full PDF.
SECTION 1 | |||||
|
|||||
Rethinking China
How manufacturers will analyze right-shoring to consider the benefits and costs of a shift in supply chains away from China and toward other countries. |
|||||
Even before COVID-19, companies were considering whether China continued to make sense for their offshore manufacturing operations.
The U.S.-China trade war caused a sudden and substantial increase in the cost of imported Chinese goods, which catalyzed a shift in U.S. supply chains away from China and toward other countries. In 2019, the total manufactured goods imported to the United States from low-cost countries in Asia (including China), as a percentage of U.S. manufacturing gross output, declined for the first time since 2011.1 This decline is attributed to reduced imports from China and appears to be correlated with the ongoing U.S.-China trade war.
The global COVID-19 pandemic accelerated and compounded these trends by exposing additional supply chain vulnerabilities. Chief among them was an overreliance on a single, primary source of supply. As some observers correctly note, companies that previously diversified their international supplies in response to the U.S.-China trade war were better positioned to mitigate the effects of the pandemic. But, when a company decides to reduce its reliance on China, where does it go?
To determine the right mix of geographic locations for its operations, a company might engage in a “right-shoring” or “best-shoring” analysis, in which a company assesses the most appropriate and effective geographic location or locations for its processes. Right-shoring is a fact-specific analysis driven by commercial, operational, tax, legal, and regulatory conditions in that company’s industry and for that company’s particular product.
Click here for more on right-shoring and considerations for rethinking China.
SECTION 2 | |||||
|
|||||
Resiliency Review
How manufacturers will review processes to ensure a stable and resilient supply chain, focusing on traceability and continuity of supply through diversification or other viable strategies. |
|||||
Post-COVID-19, companies are assessing their supply chain processes to determine areas to strengthen and ways to mitigate risk in the future.
The goal is to ensure a stable and resilient supply chain with key focuses on traceability and continuity of supply through diversification or other viable strategies. To assist companies in identifying significant risks and opportunities which can be addressed through a phased approach and prioritized plan to implement changes, we have developed a customized, on-line assessment tool (link to the right). It describes risks and related considerations each company should review regarding supply chain process changes across five key categories:
- Just in Time (JIT) Production Model
- Single Source Production Scenarios
- Contractual Allocation of Risk/Force Majeure
- Shipping, Warehousing and Inventory Processes
- In-Housing Certain Operations and Services
Each category is further described in the pages that follow. Upon accessing the on-line assessment tool, you’ll have the opportunity to consider impacts specific to your company, including: Probability of Occurrence (PO) and Probability of Benefit from Change (POBFC), upon which the tool will calculate a Priority Value (PV). You’ll receive a priority level indicator of the importance for your company to address potential issues, and implement viable process change. Customized summary results can be e-mailed (and note that no data is stored).
Click here to access the on-line assessment tool.
Click here for more on the framework to assess and update supply chain processes.
SECTION 3 | |||||
|
|||||
Innovation & Efficiency The accelerated use of new technologies and business processes to facilitate innovation and efficiencies. |
|||||
The use of new technologies and business processes to facilitate innovation and efficiency in the supply chain has been an evergreen process for decades.
Many exciting new technologies and innovative processes have emerged in the last few years, though widespread adoption in the supply chain has been slow as companies manage competing business imperatives and priorities. The coronavirus and its global impact on supply chain and production issues underscored the importance of supply chain resilience. We expect that the lessons learned from coronavirus impacts will accelerate the adoption of certain technologies below to aid in managing enterprise supply chains and production.
We also project that funding priorities within organizations will be adjusted to elevate investments that respond to supply chain resilience issues. To further assist with that prioritization, we examine several areas of innovation and efficiency in supply chain, and provide our guidance on how the various areas and technologies stack up against each other on the following measures: resilience, cost, and maturity. Our findings are shown in the adjacent graph.
1. End-to-End Connectivity/Data Exchange in the Supply Chain
Resilience | |||||||||
Cost | |||||||||
Maturity | |||||||||
|
|||||||||
1 | 2 | 3 | 4 | 5 | 6 | 7 | 8 | 9 | 10 |
Click here for more on end-to-end connectivity/data exchange in the supply chain.
2. Robots and Cobots
Resilience | |||||||||
Cost | |||||||||
Maturity | |||||||||
|
|||||||||
1 | 2 | 3 | 4 | 5 | 6 | 7 | 8 | 9 | 10 |
Click here for more on robots and cobots.
3. Upskilling Workers
Resilience | |||||||||
Cost | |||||||||
Maturity | |||||||||
|
|||||||||
1 | 2 | 3 | 4 | 5 | 6 | 7 | 8 | 9 | 10 |
Click here for more on upskilling workers.
4. Artificial Intelligence, Big Data, and Advanced Analytics
Resilience | |||||||||
Cost | |||||||||
Maturity | |||||||||
|
|||||||||
1 | 2 | 3 | 4 | 5 | 6 | 7 | 8 | 9 | 10 |
Click here for more on artificial intelligence, big data, and advanced analytics.
5. Reconfigurable Manufacturing
Resilience | |||||||||
Cost | |||||||||
Maturity | |||||||||
|
|||||||||
1 | 2 | 3 | 4 | 5 | 6 | 7 | 8 | 9 | 10 |
Click here for more on reconfigurable manufacturing.
6. Driverless Transportation
Resilience | |||||||||
Cost | |||||||||
Maturity | |||||||||
|
|||||||||
1 | 2 | 3 | 4 | 5 | 6 | 7 | 8 | 9 | 10 |
Click here for more on driverless transportation.
7. 3D Printing
Resilience | |||||||||
Cost | |||||||||
Maturity | |||||||||
|
|||||||||
1 | 2 | 3 | 4 | 5 | 6 | 7 | 8 | 9 | 10 |
Click here for more on 3D printing.
8. Creating Indirect Services Resiliency with Supplier Marketplaces Using Performance-Based Contracts
Resilience | |||||||||
Cost | |||||||||
Maturity | |||||||||
|
|||||||||
1 | 2 | 3 | 4 | 5 | 6 | 7 | 8 | 9 | 10 |
Click here for more creating indirect services resiliency with supplier marketplaces using performance-based contracts.
————————————————————
1 See Patrick Van den Bossche et al., Trade War Spurs Sharp Reversal in 2019 Reshoring Index, Foreshadowing COVID-19 Test of Supply Chain Resilience, KEARNEY, last visited June 12, 2020).