Supply Chain Disruptions in the Energy Industry: Challenges with the Supply of Lithium-ion Batteries
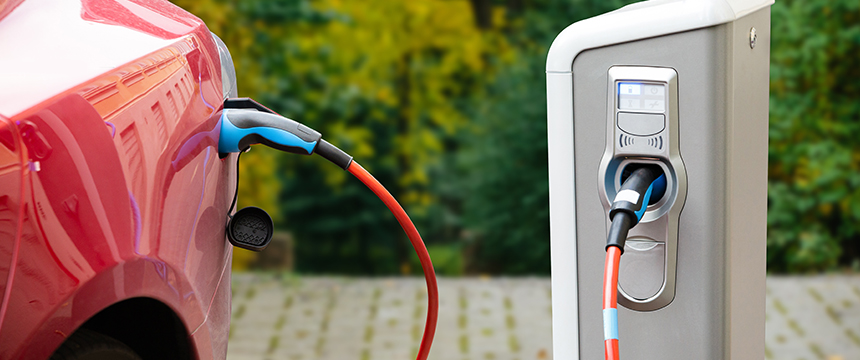
With the push toward clean energy and increased demand for electric vehicles, manufacturers need batteries — specifically lithium-ion batteries — more than ever. Examples of the accelerating transition to battery powered vehicles are everywhere: the United States Postal Service announced at least 40% of its Next Generation Delivery Vehicles and other commercial vehicles will be electric vehicles, Amazon has begun using Rivian delivery vans in over a dozen cities, and Walmart executed an agreement to purchased 4,500 electric delivery vans. With each of these conversions, the strain on the supply chain for batteries intensifies. This article will provide an overview of the lithium-ion battery industry and the current supply chain issues affecting the production and future of these batteries.
I. Lithium-Ion Battery Overview
The lithium-ion battery industry relies heavily on the mining of raw materials and production of the batteries—both of which are vulnerable to supply chain interference.
Lithium-ion batteries are mainly comprised of four key components: a cathode, anode, separator, and electrolyte, as shown in Figure 1. At a high level, the cathode (the component that produces lithium ions) is composed of lithium oxide.1 The anode (the component that stores the lithium ions) is generally made from graphite. The electrolyte is a medium that allows the free movement of the lithium ions that is composed of salts, solvents, and additives. Finally, the separator is the absolute barrier between the cathode and anode.
The cathode is the critical component relevant to this article because this is where supply chain issues are most likely to arise. The composition of the cathode depends heavily on the application of the battery.2
Application | Required Elements |
Cell Phones Cameras Laptops |
Cobalt and Lithium |
Power Tools Medical Equipment |
Manganese and Lithium or Nickel-Cobalt-Manganese and Lithium or Phosphate and Lithium |
Given the prevalence and continued demand for new cell phones, cameras, and computers, cobalt and lithium are the most valuable raw materials in the production of lithium-ion batteries and are already facing supply chain interruptions today.
There are three crucial stages in the production of lithium-ion batteries: (1) mining for raw materials, (2) refining the raw materials, and (3) producing and manufacturing the batteries themselves. At each of these stages, there are supply chain issues that should be addressed during contractual negotiations rather than waiting for the issues to arise during the course of production.
II. Supply Chain Issues within the Battery Industry
A. Production
China currently dominates the global lithium-ion battery supply chain, producing 79% of all lithium-ion batteries that entered the global market in 2021.3 The country further controls 61% of global lithium refining for battery storage and electric vehicles4 and 100% of the processing of natural graphite used for battery anodes.5 China’s dominant position in the lithium-ion battery industry and associated rare earth elements is cause for concern both to companies and governments.
COVID-19, the war in Ukraine, and inevitable geopolitical unrest will continue to affect global supply chains. Just like any other industry, the energy sector has been and will continue to be impacted by these factors. Cobalt, lithium, and nickel—critical materials in the production of batteries—are exposed to supply chain risks because production and processing are geographically concentrated and dominated by jurisdictions that have been alleged to violate labor and human rights. For additional information, see our article on Managing Supply Chain Disruption in an Era of Geopolitical Risk.
Argentina is also on the forefront of the global scramble for lithium as it currently accounts for 21% of the world’s reserves with only two mines in operation.6 Similar to China, Argentina wields significant power in the mining of raw materials and plans to expand its influence further in the lithium supply chain, with thirteen planned mines and potentially dozens more in the works.
European countries are also increasing their production, with the European Union poised to become the second largest producer of lithium-ion batteries in the world by 2025 with 11% of the global production capacity.7
Despite recent efforts,8 the United States does not have a significant presence in the mining or refining of rare earth metals. Because of this, the United States heavily relies on foreign sources to produce lithium-ion batteries. In June 2021, the U.S. Department of Energy (DOE) published a review of the large-capacity battery supply chain and recommended establishing domestic production and processing capabilities for critical materials to support a fully domestic battery supply chain.9 The DOE determined that multiple energy technologies are highly dependent on insecure and unstable foreign sources—necessitating domestic growth of the battery industry.10 In response, the DOE issued two notices of intent in February 2022 to provide $2.91 billion to boost U.S. production of lithium-ion batteries that are critical to growing the energy sector.11 The DOE intends to fund refining and production plants for battery materials, recycling facilities, and other manufacturing facilities.
New technology will also change the landscape of lithium-ion battery production. Lilac Solutions, a California-based startup company, offers technology that can recover12 up to twice as much lithium as traditional methods.13 Similarly, Princeton NuEnergy is another startup that has developed an inexpensive, sustainable way to make new batteries from old ones.14 Although this type of new technology will ease the supply chain bottleneck, it does not change the fact that lithium-ion battery production heavily relies on raw source material availability. The bottom line remains that the world’s existing lithium production is concentrated in Chile, Australia, Argentina, and China.15 As indicated in Figure 2 below, the reliance on foreign-sourced materials is likely to continue for the next few years until further development of battery technology that does not rely on rare earth metals.
Figure 2: Future Lithium Production Sources
B. Price
In a separate article, Foley’s Lauren Loew discussed how the price surge of lithium reflects increased battery demands, with the cost rising more than 900% since 2021.16 These price surges continue as inflation remains at an all-time high. The rising costs of lithium-ion batteries, coupled with inflation, have already resulted in increases in the prices for electric vehicles. For additional information on the impact of inflation on the supply chain, see our article Inflation Woes: Four Key Ways for Companies to Address Inflation in the Supply Chain.
Decision makers will want to be aware of the impact of inflation on their contracts involving lithium-ion batteries. “In well-established energy storage markets, like the U.S., higher costs have resulted in some developers looking to renegotiate contract prices with offtakers. These renegotiations can take time and delay project commissioning.” says Helen Kou, an energy storage associate at the research company BloombergNEF.17
C. Transportation/Flammability
Lithium-ion batteries are regulated as a hazardous material under the U.S. Department of Transportation’s (DOT) Hazardous Materials Regulations by the U.S. Department of Transportation Pipeline and Hazardous Materials Safety Administration (PHMSA). Unlike standard batteries, most lithium-ion batteries contain flammable materials and have an incredibly high energy density. As a result, the lithium-ion batteries can overheat and ignite under certain conditions, such as a short circuit, physical damage, improper design, or assembly. Once ignited, lithium cell and battery fires can be difficult to extinguish.18 As a result, companies need to be aware of the potential risks and evaluate the proper precautions when engaged in transactions involving lithium-ion batteries.
To date, there is no conclusive research to determine if electric vehicles are more prone to spontaneous fires compared to traditional vehicles.19 Research shows that electric vehicles only have a 0.03% chance of igniting, compared to traditional combustion engines at 1.5% chance of igniting.20 Hybrid vehicles—which have a high voltage battery and an internal combustion engine—have the greatest likelihood of a vehicle fire at 3.4%.21
On February 16, 2022, a cargo ship carrying nearly 4,000 vehicles from Germany to the United States caught fire in the Atlantic Ocean.22 Nearly two weeks later, the cargo ship sank in the middle of the Atlantic. Although there is no official statement as to the breakdown of traditional and electric vehicles on board, the lithium-ion battery vehicles would have made the fires harder to extinguish.
III. Conclusion
As the world moves toward cleaner energy, questions and issues involving the supply chain will grow. These questions should be addressed as soon as possible before executing any contract. If you or your company are involved in transactions where lithium-ion batteries are a material component, there are significant supply chain hurdles that should be addressed early on during negotiations regarding the sourcing of raw materials and pricing issues. In light of the limited availability of raw materials and the complexities involved in developing lithium mines, companies ought to look to alternative avenues for obtaining lithium and other critical components. Companies relying on lithium-ion batteries should evaluate and invest in technology that is economically viable and maximizes the viability and recyclability of these batteries to avoid supply-chain issues. Alternatively, companies can enter into multi-year agreements for lithium. However, given the heavy reliance on rare earth metals to produce lithium-ion batteries, companies ought to heavily consider the sourcing of the metals and other issues that may affect mining and refining, such as geopolitical issues. If you have any questions about issues concerning supply chain issues, please contact our team at Foley & Lardner.
Subscribe to the Supply Chain Disruption Series
To help you navigate these uncharted territories in supply chain, we invite you to subscribe to Foley’s Supply Chain Disruption series by clicking here.
1 Samsung SDI, The Four Components of a Li-Ion Battery (last visited Aug. 1, 2022).
2 Spangenberger, Jeff, Introduction to Lithium Ion Batteries (Mar. 22, 2008).
3 Statista, Share of the Global Lithium-Ion Battery Manufacturing Capacity in 2021 with a Forecast for 2025, by Country (last visited Aug. 1, 2022).
4 Cohen, Ariel, America Trails in Global Race for Rare Earth Metals, Forbes (Mar. 21, 2021),
5 Id.
6 Nugent, Ciara, New Lithium Mining Technology Could Give Argentina a Sustainable Gold Rush, Time (July 26, 2022).
7 DW, EU plans millions of e-vehicle batteries, jobs by 2025 (Mar. 23, 2021); Statista, Share of the Global Lithium-Ion Battery Manufacturing Capacity in 2021 with a Forecast for 2025, by Country (last visited Aug. 1, 2022).
8 See Lipton, Eric, Penn, Lithium Mining Race, New York Times (May 6, 2021).
9 The White House, Building Resilient Supply Chains, Revitalizing American Manufacturing, and Fostering Broad-Based Growth—100-Day Reviews Under Executive Order 14017 (2021).
10 U.S. Department of Energy, America’s Strategy to Secure the Supply Chain for a Robust Clean Energy Transition (2022).
11 U.S. Department of Energy, Biden Administration, DOE to Invest $3 Billion to Strengthen U.S. Supply Chain for Advanced Batteries for Vehicles and Energy Storage (Feb 11, 2022),
12 Recovery is the process by which lithium, cobalt, nickel, and manganese can be retrieved from batteries that no longer have a useful life. After these metals are recovered, they can be repurposed into new batteries.
13 Id.
14 Seltzer, Molly, A Better Way to Recycle Lithium Batteries Is Coming From This Princeton Startup, Princeton: Andlinger Center for Energy and Development (Mar. 3, 2022).
15 Volkswagen, Lithium Mining: What You Should Know About the Contentious Issue.
16 Nicholls, Mark, Inflation Bites at the Battery Storage Bonanza, Energy Monitor (June 10, 2022).
17 Id.
18 U.S. Department of Transportation, Pipeline and Hazardous Materials Safety Admin., Transporting Lithium Batteries, (last visited Aug. 1, 2022).
19 Winton, Neil, Electric Car Fire Risks Look Exaggerated, But More Data Required For Definitive Verdict, Forbes (Mar. 2, 2022).
20 Putzer, Mark, Electric Vehicles Catch Fires Considerably Less Than Gas Cars, Motor Biscuit (Feb. 13, 2022).
21 Evers, Andrew, and Kolodny, Lora, Electric Vehicle Fires Are Rare, But Hard To Fight—Here’s Why, CNBC (Jan. 29, 2022).
22 Franklin, Jonathan, A Burning Cargo Ship Full of Porsches and VWs is Adrift in the Mid- Atlantic, NPR (Feb. 17, 2022).